Heavy Duty Buffer
Expertly Crafted Rubber Cylindrical Mounts, Ensuring Stability and Durability
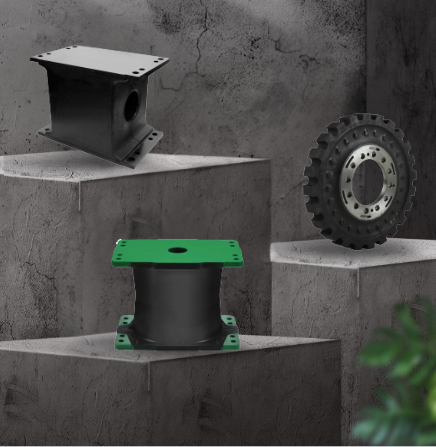
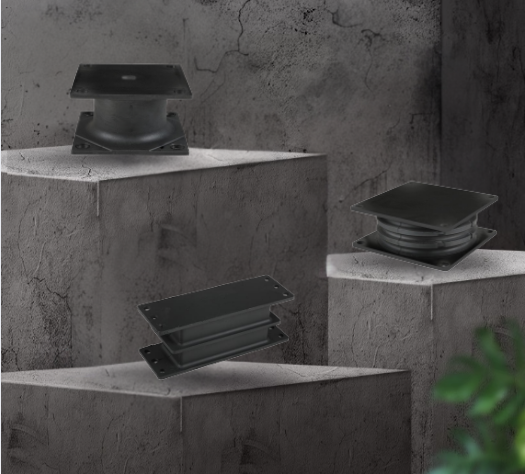
Our products
Heavy Duty Buffer
- SW Series Multi-Layer Antivibration Dampers
- SWA Series Multi-Layer Antivibration Dampers
- TEE Series Multi-Layer Antivibration Dampers
- LZQ Series Coupling Components
- TE Series Large Piling Elastomers
Product Showcase
Precision-Engineered Rubber Buffers You Can Trust
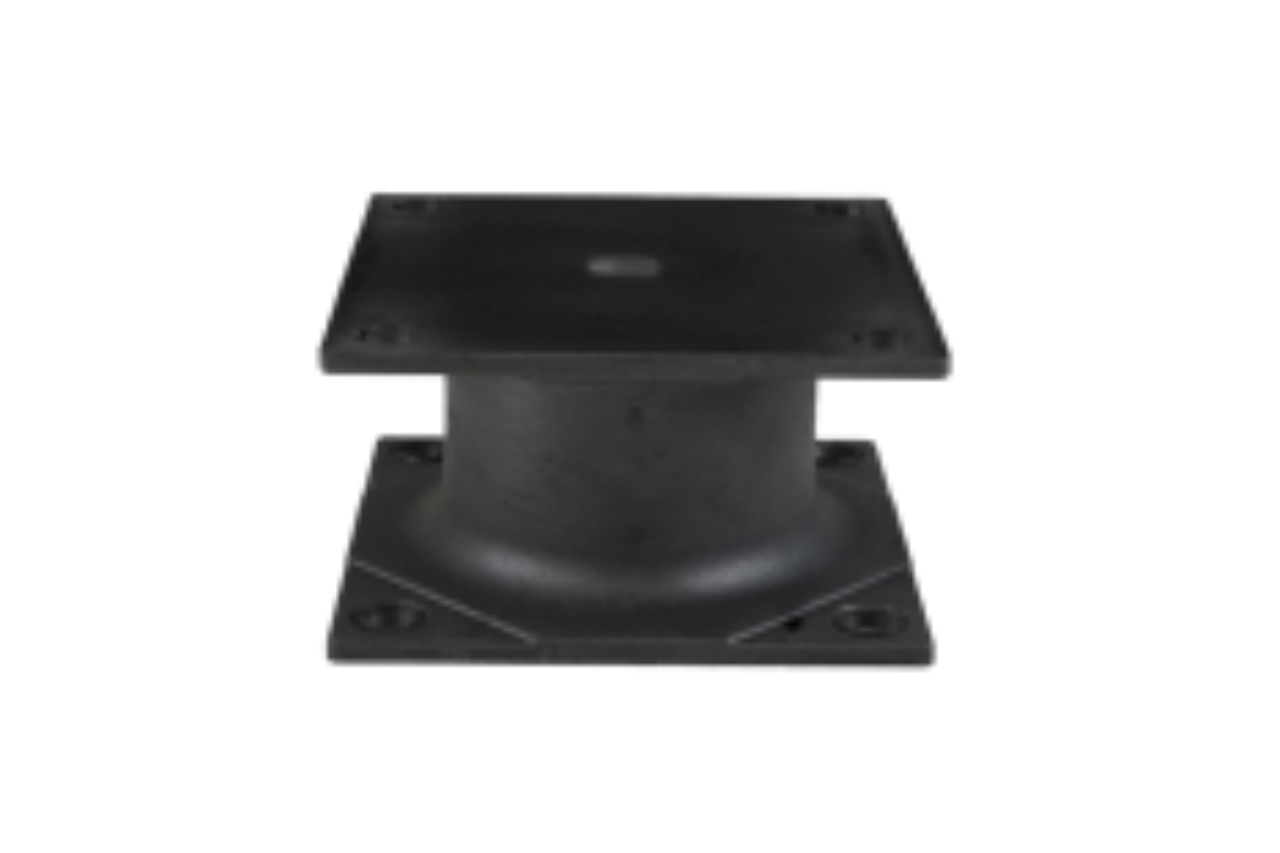
Antivibration Dampers
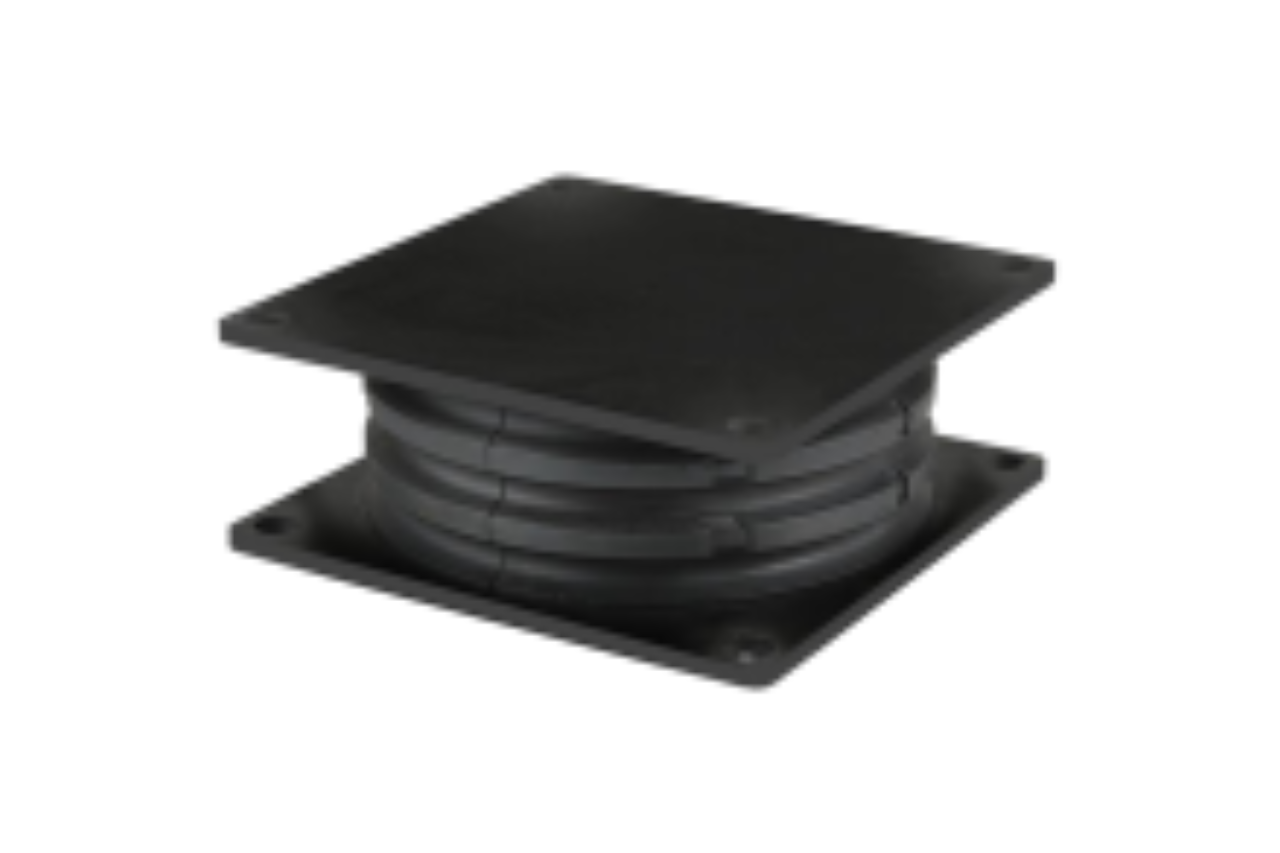
Antivibration Dampers
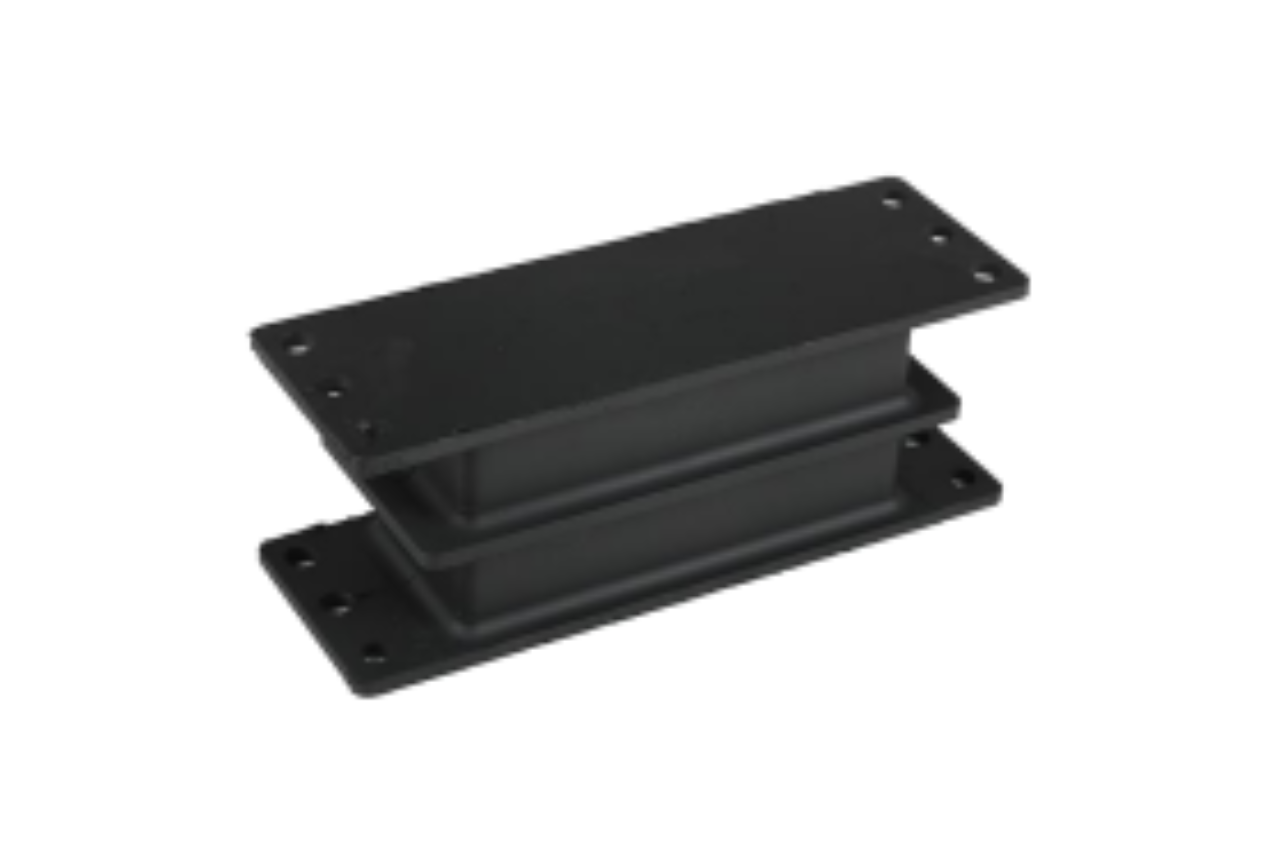
Antivibration Dampers
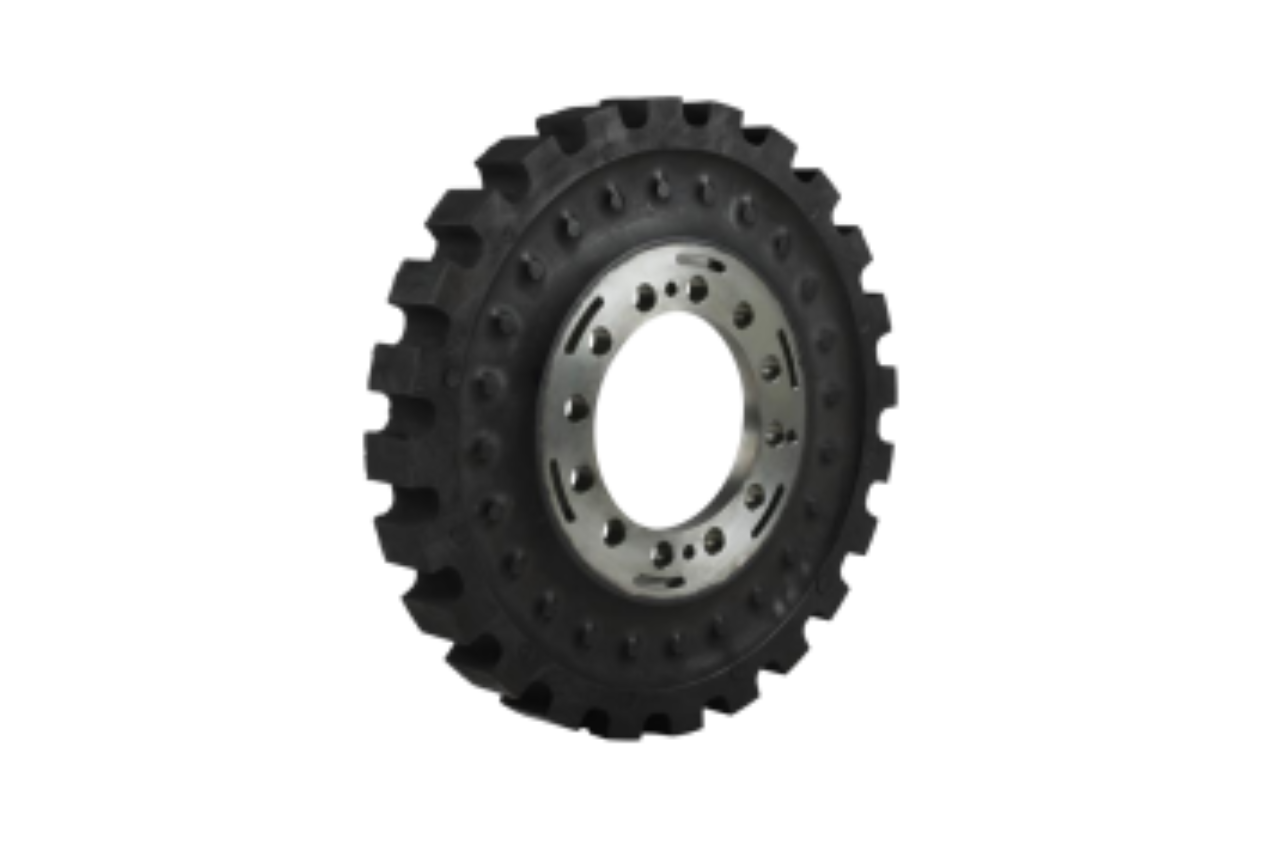
Coupling Components
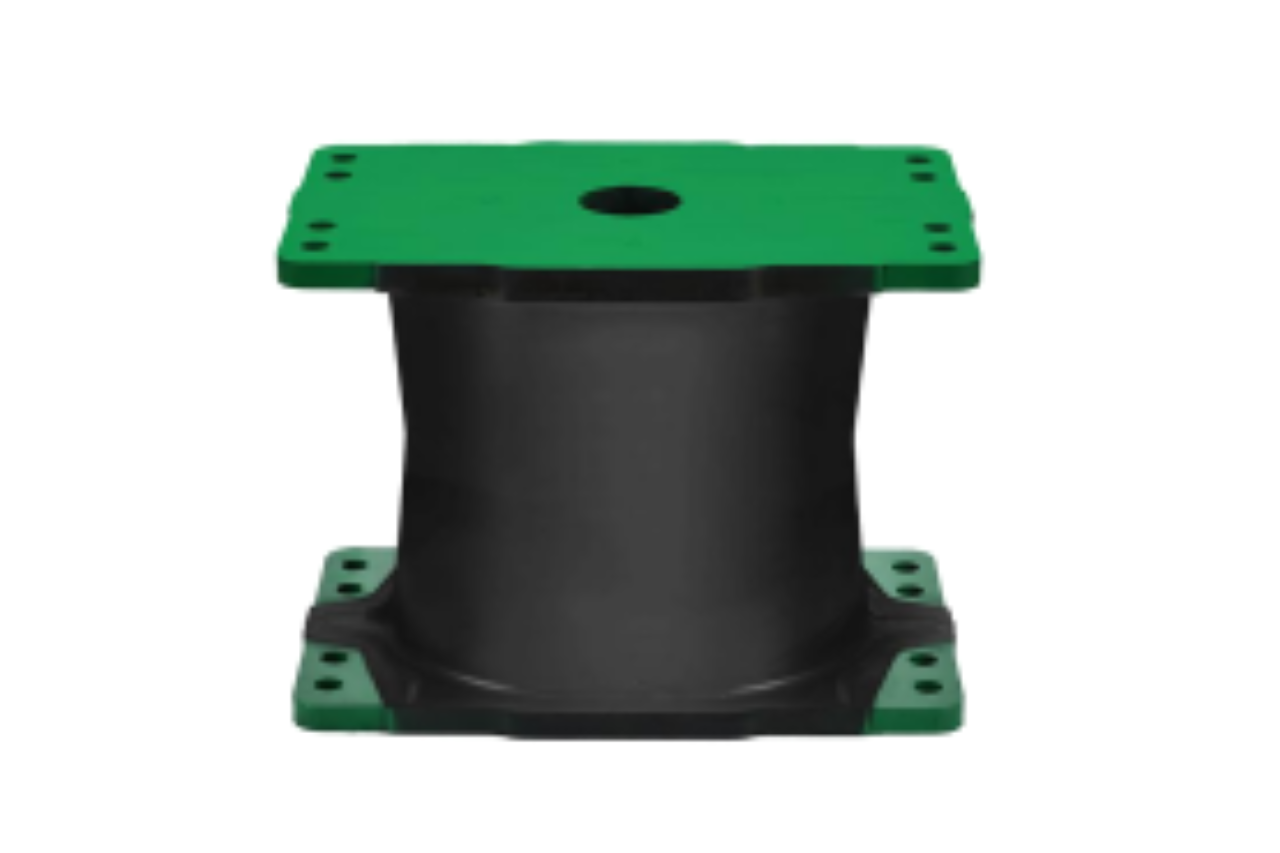
Piling Elastomers
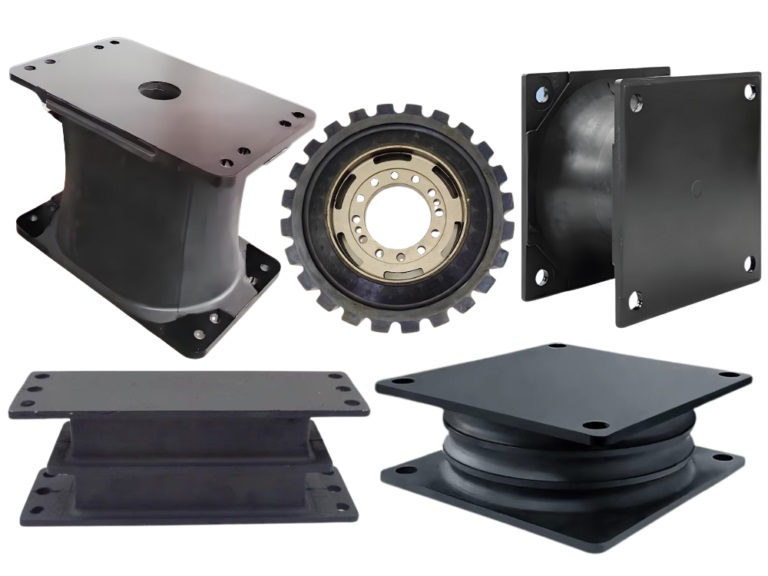
Customizable
Why Choose Us
Trusted Rubber Vibration Isolator Manufacturer with 30 Years of Expertise
Factory-direct solutions with natural rubber, customizable options, reliable quality, and trusted performance.
We own and operate our factory, ensuring strict quality control, stable lead times, and support for small-batch customization
With over three decades in vibration isolation, we offer trusted solutions backed by rich technical knowledge and real-world application.
Our isolators use pure natural rubber for excellent elasticity, durability, and superior shock absorption compared to synthetic materials.
Our ISO-compliant production lines and testing systems ensure consistent quality and reliable performance across all batches.
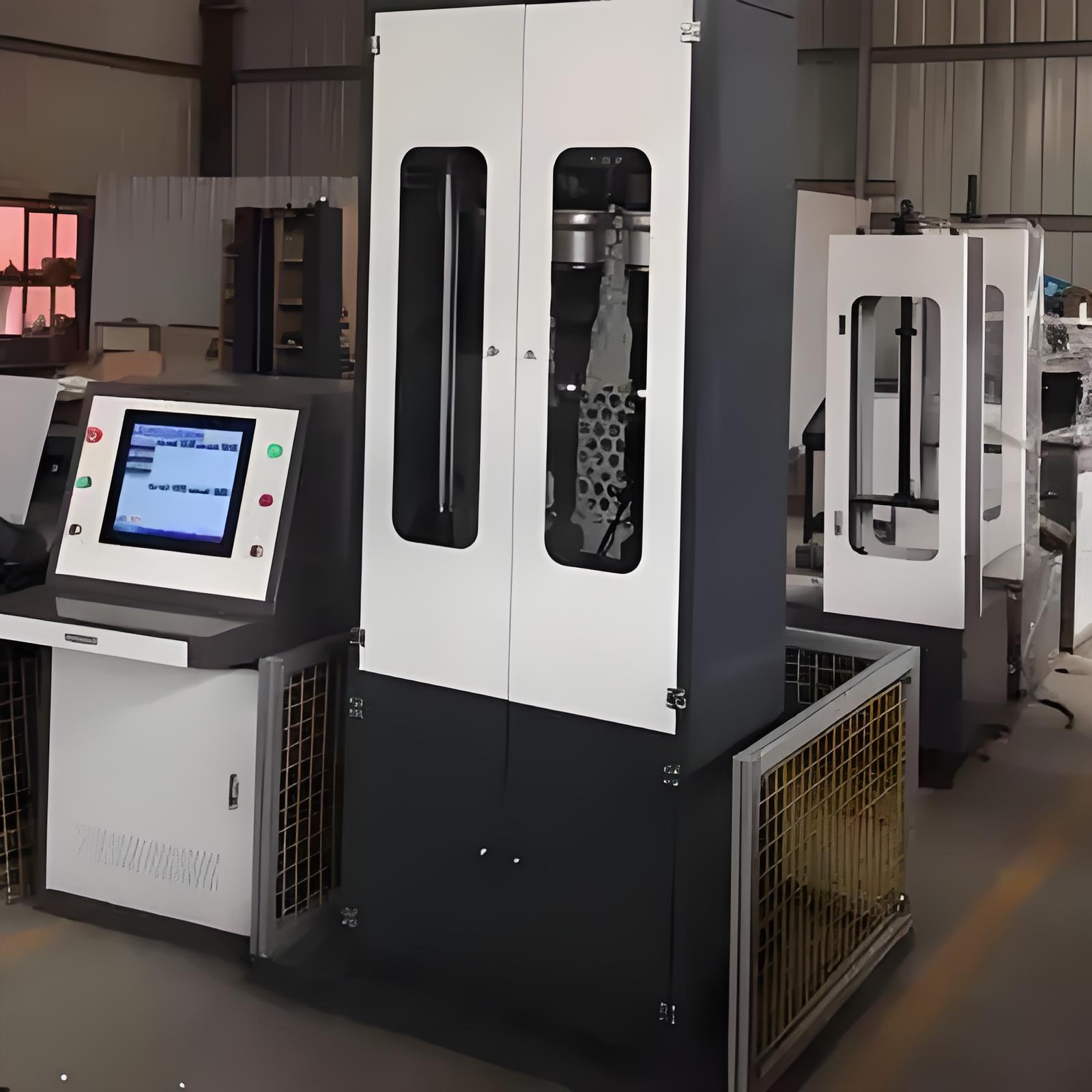
+86 13032112360
Common Questions
Most Popular Questions
The Role of Heavy-Duty Buffers in Industrial Machinery
Heavy-duty buffers play an essential role in protecting industrial machinery from shock, impact, and vibration. In the demanding environments of factories, construction sites, or transport systems, machines are constantly exposed to dynamic forces that can cause mechanical stress, structural fatigue, and ultimately failure. A heavy-duty buffer is specifically engineered to absorb these forces and prevent damage.
Energy Absorption and Impact Damping
At its core, the heavy-duty buffer functions as an energy absorber. When machinery operates—particularly under heavy load conditions—there are often sudden stops, collisions, or repetitive impacts. These generate mechanical energy that, if not properly managed, can be transmitted directly into key components like bearings, motors, gears, and mounting structures. Over time, this leads to wear and premature equipment failure. The buffer intercepts that energy, disperses it safely, and reduces the stress on critical parts.
Enhancing Operational Safety
Another key purpose of the heavy-duty buffer is to enhance safety. Industrial equipment that stops abruptly or shifts suddenly due to unabsorbed impact can endanger workers and other equipment nearby. By cushioning these movements, buffers make mechanical transitions smoother and significantly reduce the risk of accidents. This is particularly important in high-stakes applications such as elevators, cranes, and railway systems.
Extending Equipment Lifespan
Furthermore, heavy-duty buffers contribute to longer equipment lifespan and reduced maintenance needs. By minimizing the repeated shock loads, buffers help avoid micro-damage that accumulates over time. This reduces the frequency of repairs and extends the operational period of machines, making them more reliable and cost-effective to operate.
Supporting Stability in High-Load Operations
These buffers also ensure better operational stability. Machines subjected to continuous or high-frequency vibration can perform inconsistently or lose alignment. A well-designed buffer dampens such vibrations and enables the machine to function precisely, even in high-load or high-speed applications.
Conclusion
In summary, the primary purpose of a heavy-duty buffer is to protect industrial machinery from impact and vibration, improving safety, reliability, and longevity. Without them, the performance and durability of machines would be compromised, especially in environments where operational forces are extreme.
Heavy-duty buffers are designed to withstand harsh working conditions and absorb significant mechanical impacts. Choosing the right materials is crucial for ensuring their durability, energy absorption capacity, and overall performance. Various materials are selected based on the specific application, load requirements, and environmental factors.
Rubber Compounds for Shock Absorption
One of the most common materials used in heavy-duty buffers is rubber. Rubber’s natural elasticity and high damping properties make it excellent for absorbing shocks and vibrations. Different rubber compounds such as neoprene, natural rubber, and nitrile rubber are often used, each offering unique benefits. Neoprene, for example, is resistant to oils, weathering, and temperature variations, making it suitable for outdoor and industrial environments.
Metal Components for Structural Strength
While rubber handles energy absorption, metal parts provide structural integrity to the buffer. Steel or stainless steel is often used for the core and mounting elements due to their strength and resistance to deformation. These metals ensure that the buffer maintains its shape and position under heavy loads and repeated impacts.
Polyurethane for Durability and Wear Resistance
Polyurethane is another material frequently used in heavy-duty buffers, particularly where abrasion resistance and long service life are required. It offers better tear resistance and hardness compared to rubber, which makes it ideal for environments with abrasive particles or harsh mechanical wear.
Composite Materials and Multi-Layer Designs
Some heavy-duty buffers use composite materials or combine different layers to optimize performance. Multi-layer designs can incorporate rubber and metal or rubber and polyurethane layers to balance flexibility, strength, and energy dissipation. This layered approach allows buffers to be tailored for specific operational demands.
Environmental Considerations in Material Selection
In addition to mechanical properties, environmental factors like temperature extremes, exposure to chemicals, and UV radiation influence material choice. For instance, rubber buffers used outdoors may be formulated with additives to resist ozone cracking and UV degradation, ensuring longer service life.
Conclusion
The choice of materials in heavy-duty buffers is critical to their effectiveness and longevity. By combining elastomers like rubber or polyurethane with strong metals and using innovative composite designs, manufacturers can produce buffers capable of handling demanding industrial applications while maintaining durability and performance.
Common Applications of Heavy-Duty Buffers
Heavy-duty buffers are widely used across various industries due to their ability to absorb shock, reduce vibration, and protect equipment from damage. Their robustness and durability make them ideal for harsh environments and heavy load conditions.
Industrial Machinery and Manufacturing
One of the primary applications of heavy-duty buffers is in industrial machinery and manufacturing equipment. They are installed in presses, stamping machines, conveyors, and automated production lines to cushion sudden stops and prevent mechanical damage. Buffers help maintain operational stability and prolong machine life.
Transportation and Rail Systems
Heavy-duty buffers are critical components in transportation, especially in rail systems. Train couplers, bumpers, and buffers on railway cars use these devices to absorb impact forces during coupling and braking, reducing wear and ensuring passenger safety. Similarly, in heavy trucks and commercial vehicles, buffers help reduce shock loads from road irregularities.
Construction and Material Handling Equipment
Construction machinery such as cranes, excavators, and forklifts utilize heavy-duty buffers to absorb shocks from dynamic loads and operational impacts. This protects sensitive hydraulic and mechanical components, improving equipment reliability and operator safety.
Energy Sector Equipment
In power plants and renewable energy installations, heavy-duty buffers are used to protect turbines, generators, and heavy pumps from vibration and impact forces. These buffers contribute to smoother operation and reduce maintenance frequency in critical energy infrastructure.
Aerospace and Defense Applications
Heavy-duty buffers are also found in aerospace and defense equipment where they help absorb the shock from launches, landings, and mechanical operations. Their use ensures equipment integrity and reliability in extreme conditions.
Conclusion
Heavy-duty buffers serve a vital function in numerous industries by safeguarding machinery and equipment from impact and vibration. Their diverse applications—from manufacturing to transportation and energy—highlight their importance in maintaining safety, performance, and durability in demanding environments.
Differences Between Heavy-Duty Buffers and Standard Buffers
Heavy-duty buffers and standard buffers both serve the purpose of absorbing shock and reducing vibration in machinery and equipment. However, they differ significantly in terms of design, materials, capacity, and application.
Load Capacity and Durability
The most noticeable difference lies in their load-bearing capacity. Heavy-duty buffers are designed to handle much higher loads and more severe impact forces than standard buffers. They use tougher materials and more robust construction to withstand harsh industrial environments and heavy usage.
Material Composition
Heavy-duty buffers often incorporate reinforced rubber compounds, polyurethane, and stronger metals such as stainless steel or high-grade steel. Standard buffers, on the other hand, may use simpler rubber or plastic materials suitable for lighter applications.
Size and Structure
Heavy-duty buffers tend to be larger and more complex in structure, sometimes featuring multi-layer or composite designs to enhance energy absorption and longevity. Standard buffers are typically smaller and simpler, adequate for less demanding tasks.
Application Scope
While standard buffers are commonly found in consumer products, light machinery, or office equipment, heavy-duty buffers are specifically engineered for industrial machinery, heavy vehicles, construction equipment, and other high-stress applications.
Maintenance and Lifespan
Heavy-duty buffers generally have a longer lifespan and require less frequent replacement due to their reinforced materials and design. Standard buffers may wear out faster under comparable conditions and need more regular maintenance.
Conclusion
In summary, heavy-duty buffers differ from standard buffers mainly in strength, durability, material quality, size, and application. Selecting the right type depends on the specific requirements of the machinery and the working environment.
Heavy-duty buffers are critical components in protecting machinery and equipment from shock and vibration. Because industrial environments and applications vary widely, customization of these buffers is often necessary to meet specific operational requirements.
Tailoring Load Capacity and Size
One of the primary customization options involves adjusting the load capacity and physical dimensions of the buffer. Different machines require buffers that can handle specific weight ranges and fit within certain spatial constraints. Manufacturers can design buffers to match these exact parameters, ensuring optimal performance.
Material Selection Based on Environment
Customization also includes selecting materials that suit the environmental conditions where the buffer will be used. For example, buffers intended for high-temperature environments may use special heat-resistant rubber compounds. Buffers for chemical plants might require materials resistant to corrosive substances.
Specialized Designs for Unique Applications
Some industrial processes demand unique buffer designs, such as multi-layered buffers, integrated damping systems, or buffers combined with mounting hardware. These specialized designs improve energy absorption, reduce noise, or simplify installation based on the application’s needs.
Compliance with Industry Standards
Custom heavy-duty buffers can also be designed to comply with specific safety and industry standards, such as ISO certifications or local regulations. This ensures that the buffers are safe and reliable in their intended use.
Benefits of Customization
Customized heavy-duty buffers enhance equipment protection, extend operational lifespan, and improve safety. They provide a tailored solution that standard off-the-shelf buffers may not offer, particularly in challenging industrial conditions.
Conclusion
In summary, heavy-duty buffers can indeed be customized to meet specific industrial needs. By adjusting size, material, design, and compliance features, manufacturers provide solutions that optimize performance and durability for diverse applications.
Heavy-duty buffers play a vital role in protecting machinery from impact and vibration, but like any mechanical component, they require regular maintenance to ensure optimal performance and longevity.
Routine Inspections
Regular visual inspections are essential to check for signs of wear, cracks, or deformation in the buffer material. Early detection of damage can prevent further deterioration and unexpected failures. Inspections should also verify that mounting hardware remains secure and corrosion-free.
Cleaning and Environmental Protection
Keeping buffers clean from dust, grease, and other contaminants helps maintain their effectiveness. In harsh environments, buffers may need protective coatings or covers to shield against chemicals, UV radiation, or extreme temperatures.
Lubrication (If Applicable)
Some heavy-duty buffers with moving metal parts or integrated springs may require periodic lubrication to reduce friction and prevent corrosion. However, many rubber or polyurethane buffers are maintenance-free in this regard.
Load and Performance Monitoring
Monitoring the load and vibration levels on buffers can help identify unusual stresses or operational changes. This can be done with sensors or regular equipment performance reviews, allowing timely adjustments or replacements.
Scheduled Replacement
Even with good maintenance, heavy-duty buffers have a finite lifespan. Manufacturers typically provide recommended service intervals based on usage conditions. Following these guidelines helps avoid equipment damage due to buffer failure.
Conclusion
Proper maintenance of heavy-duty buffers ensures they continue to protect machinery effectively and extend service life. Regular inspections, cleaning, appropriate lubrication, and load monitoring are key practices for maintaining buffer performance in demanding industrial settings.
Heavy-duty buffers are essential components in industrial systems for minimizing noise and vibration, which can otherwise cause equipment damage, operator discomfort, and operational inefficiencies.
Absorbing and Damping Vibrations
Heavy-duty buffers are typically made from elastomeric materials like rubber or polyurethane that have excellent energy-absorbing properties. When machinery generates vibrations, these buffers absorb the mechanical energy, converting it into small amounts of heat, thereby reducing the amplitude of vibrations transmitted to the surrounding structure.
Isolation of Equipment from Structure
By placing heavy-duty buffers between machinery and its mounting base or frame, vibrations are isolated and prevented from spreading through the building or platform. This isolation reduces noise levels and protects adjacent equipment from vibration-induced wear.
Noise Reduction through Impact Cushioning
Buffers also cushion impacts from moving parts, sudden stops, or shocks. This cushioning effect prevents loud banging or clanking noises that commonly occur in heavy machinery, improving the acoustic environment in industrial settings.
Enhancing Operator Comfort and Safety
Reducing vibration and noise levels helps improve operator comfort and safety by minimizing fatigue and the risk of hearing damage. This also contributes to better productivity and a healthier workplace.
Customization for Optimal Noise and Vibration Control
Heavy-duty buffers can be designed or customized with specific damping properties to target particular frequency ranges of vibration or noise, allowing more precise control based on the equipment’s operating conditions.
Conclusion
In conclusion, heavy-duty buffers significantly reduce noise and vibration through energy absorption, equipment isolation, and impact cushioning, contributing to safer, quieter, and more reliable industrial operations.
Heavy-duty buffers are designed to absorb shock and reduce vibration, but like any mechanical component, they are subject to wear and failure over time. Understanding the common failure modes helps in proper maintenance and timely replacement.
Material Degradation
One of the most common failure modes is the degradation of the buffer’s elastomeric material. Exposure to harsh chemicals, UV radiation, extreme temperatures, or ozone can cause cracking, hardening, or brittleness, reducing the buffer’s effectiveness.
Mechanical Wear and Tear
Repeated impact and cyclic loading can cause mechanical wear, leading to deformation or permanent compression set in the buffer. This reduces its ability to absorb shocks and vibrations effectively.
Bonding Failure
In buffers where rubber is bonded to metal components, failure of the adhesive bond can occur. This separation compromises the structural integrity and may cause the buffer to detach from its mounting.
Corrosion of Metal Parts
Metal components in heavy-duty buffers can corrode over time, especially in humid or chemically aggressive environments. Corrosion weakens the structure and may lead to premature failure.
Improper Installation
Incorrect installation can cause uneven loading or stress concentrations, leading to early damage or failure. Ensuring proper installation according to manufacturer guidelines is crucial.
Overloading
Subjecting buffers to loads beyond their design capacity causes accelerated wear and eventual failure. Operating within specified limits is necessary to maintain buffer longevity.
Conclusion
Recognizing these common failure modes allows users to implement preventive maintenance and choose suitable buffers for their applications, ensuring reliable operation and extended service life.
Heavy-duty buffers are often deployed in challenging industrial environments, where temperature, humidity, chemicals, and other factors can significantly impact their performance and longevity.
Temperature Effects
Extreme temperatures—both high and low—can alter the physical properties of the buffer materials. High heat may cause softening or accelerated aging of rubber components, while extreme cold can make materials brittle and prone to cracking. Selecting temperature-resistant materials is crucial for reliable operation.
Chemical Exposure
Exposure to chemicals such as oils, solvents, acids, and alkalis can degrade buffer materials, especially elastomers. Chemical resistance varies by material type; therefore, choosing buffers with appropriate chemical-resistant compounds is essential for maintaining performance in corrosive environments.
UV Radiation and Ozone
Prolonged exposure to ultraviolet (UV) light and ozone can lead to the breakdown of rubber components, causing surface cracks and loss of elasticity. Buffers intended for outdoor use often incorporate UV stabilizers to prolong lifespan.
Moisture and Humidity
High humidity or immersion in water can accelerate corrosion of metal parts and promote microbial growth on buffer surfaces, potentially degrading materials. Protective coatings and proper sealing can mitigate these effects.
Mechanical Stress from Environmental Factors
Environmental vibrations, shocks, and other mechanical stresses unique to certain locations can compound wear on buffers. Proper selection and installation help buffer performance under these conditions.
Conclusion
Environmental conditions play a critical role in the effectiveness and durability of heavy-duty buffers. Understanding these factors and selecting materials and designs accordingly ensures optimal buffer function and lifespan in demanding industrial settings.
Selecting the appropriate heavy-duty buffer is crucial for ensuring effective vibration damping and equipment protection in industrial applications. Several key factors should be considered to make the best choice.
Understand the Load Requirements
First, determine the maximum load and impact forces the buffer needs to withstand. This includes both static loads and dynamic shock loads. Choosing a buffer with suitable load capacity prevents premature failure and ensures safety.
Consider Environmental Conditions
Assess the environment where the buffer will be installed, including temperature ranges, exposure to chemicals, moisture, and UV radiation. Selecting materials resistant to these conditions will enhance buffer durability.
Evaluate Size and Installation Constraints
The available space and mounting configuration often limit buffer size and shape. Choose a buffer that fits within the physical constraints without compromising performance or safety.
Analyze Vibration and Noise Reduction Needs
Identify the specific vibration frequencies and noise levels that must be controlled. Some buffers offer tailored damping characteristics for different frequency ranges, which can improve effectiveness.
Check Compliance and Standards
Ensure that the chosen buffer meets relevant industry standards, safety regulations, and quality certifications. This guarantees reliability and legal compliance.
Consult Manufacturer Expertise
Work with reputable manufacturers who provide technical support and customization options. Their expertise can help optimize buffer selection for your specific application.
Conclusion
Choosing the right heavy-duty buffer involves balancing load capacity, environmental resistance, size, damping needs, and compliance. Careful evaluation and professional guidance lead to improved equipment protection and longer service life.
Heavy-duty buffers play a crucial role in protecting machinery by absorbing shock, reducing vibration, and enhancing overall system performance. Understanding their benefits can help industries optimize equipment reliability and lifespan.
Shock Absorption
Heavy-duty buffers effectively absorb impact forces from sudden stops or collisions, protecting sensitive machine components from damage and reducing maintenance costs.
Vibration Reduction
By isolating vibrations generated during operation, these buffers minimize wear and tear on equipment, preventing premature failure and improving operational stability.
Noise Control
Heavy-duty buffers reduce noise levels by dampening mechanical vibrations and impacts, creating a safer and more comfortable working environment.
Equipment Longevity
Reducing mechanical stress and impact forces extends the life of machinery components, lowering replacement frequency and associated downtime.
Enhanced Safety
Buffers prevent excessive movements and shocks, reducing the risk of accidents and injuries in industrial settings.
Cost Savings
With decreased maintenance needs and prolonged equipment life, heavy-duty buffers contribute to significant cost savings over time.
Conclusion
Incorporating heavy-duty buffers into machinery systems offers multiple advantages including shock absorption, vibration damping, noise reduction, increased safety, and cost efficiency, making them essential for reliable industrial operations.
Heavy-duty buffers are essential components designed to enhance the safety of industrial machinery by mitigating the effects of shock, vibration, and sudden impacts.
Absorbing Impact Forces
By absorbing and dissipating energy from sudden shocks or collisions, heavy-duty buffers protect critical machine parts from damage, reducing the chance of mechanical failure that could lead to accidents.
Preventing Equipment Overtravel
Buffers limit the movement range of machinery components, preventing overtravel that could cause structural damage or unsafe conditions.
Reducing Vibration-Induced Failures
Continuous vibration can loosen fasteners and cause fatigue cracks. Buffers reduce vibration levels, helping maintain the integrity and safety of equipment.
Minimizing Operator Hazards
Lower vibration and noise levels improve working conditions, reducing operator fatigue and the risk of errors or accidents.
Compliance with Safety Standards
Using appropriate buffers helps meet safety regulations and standards, ensuring legal compliance and workplace safety.
Conclusion
Heavy-duty buffers contribute significantly to equipment safety by absorbing shocks, controlling movements, reducing vibrations, and improving operator conditions, making them vital for safe industrial operations.