Rubber Cylindrical Mounts
Expertly Crafted Rubber Cylindrical Mounts, Ensuring Stability and Durability
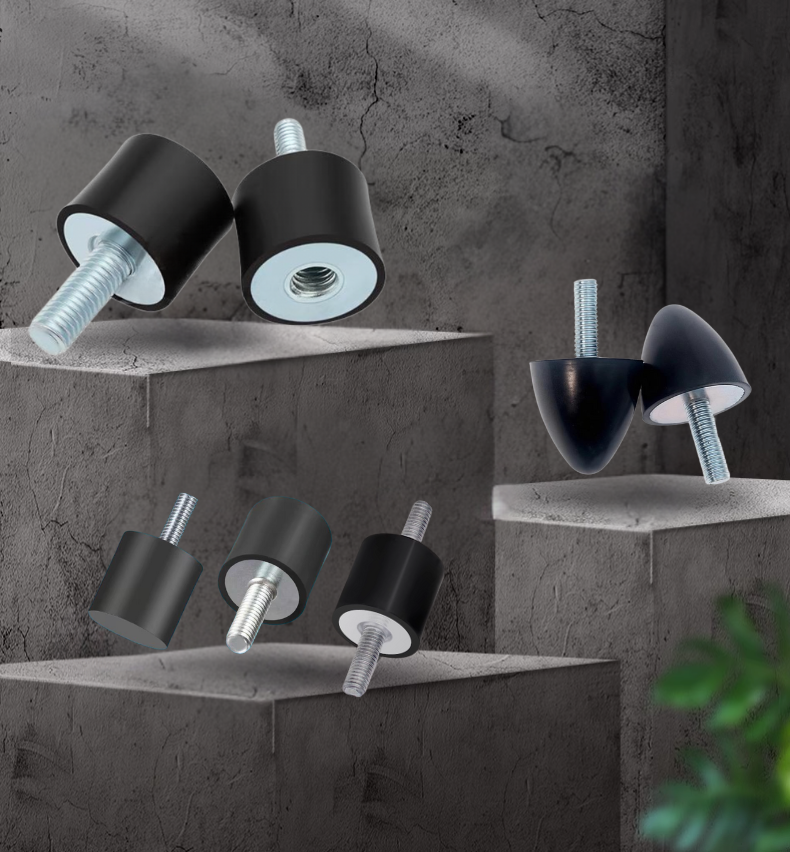
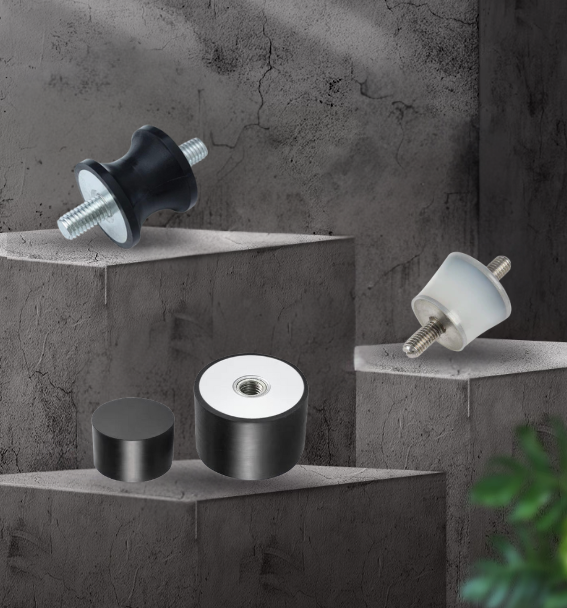
Our products
Rubber Cylindrical Mounts
- JNDE Type Cylindrical Mounts
- JNDD Type Cylindrical Mounts
- JNBC Type Cylindrical Mounts
- JNBE Type Cylindrical Mounts
- SJDP Type Cylindrical Mounts
- GVV Type Cylindrical Mounts
- VVS Type Cylindrical Mounts
Product Showcase
Precision-Engineered Rubber Buffers You Can Trust
Cylindrical Mounts
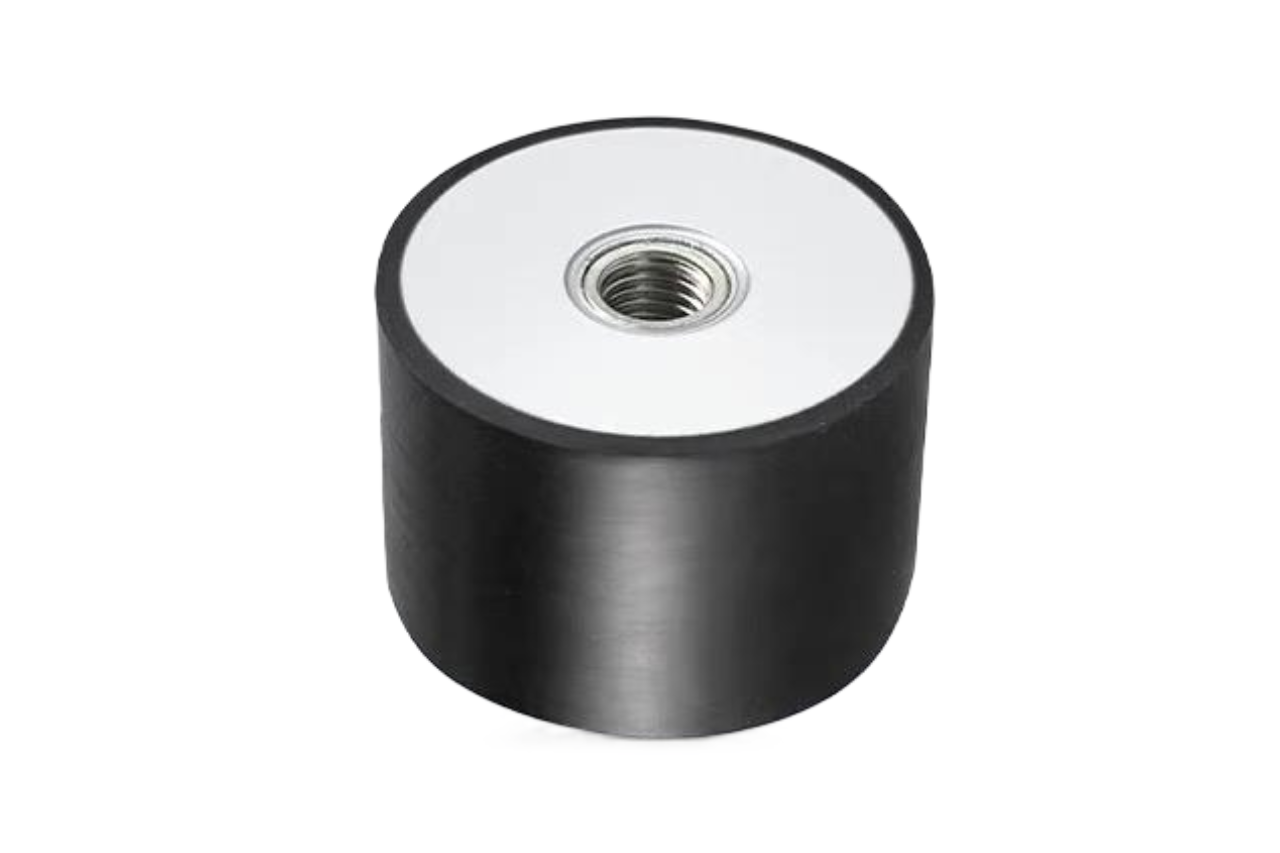
Cylindrical Mounts
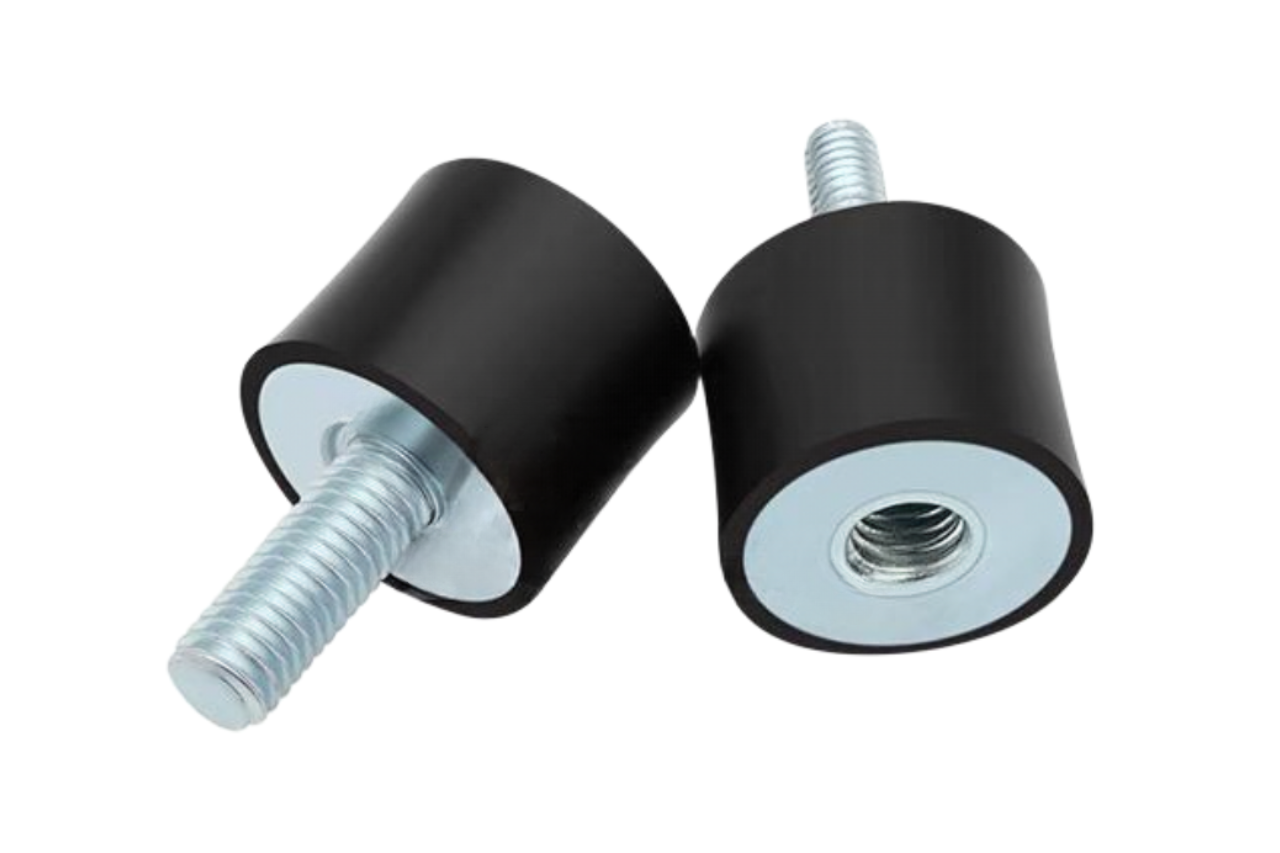
Cylindrical Mounts
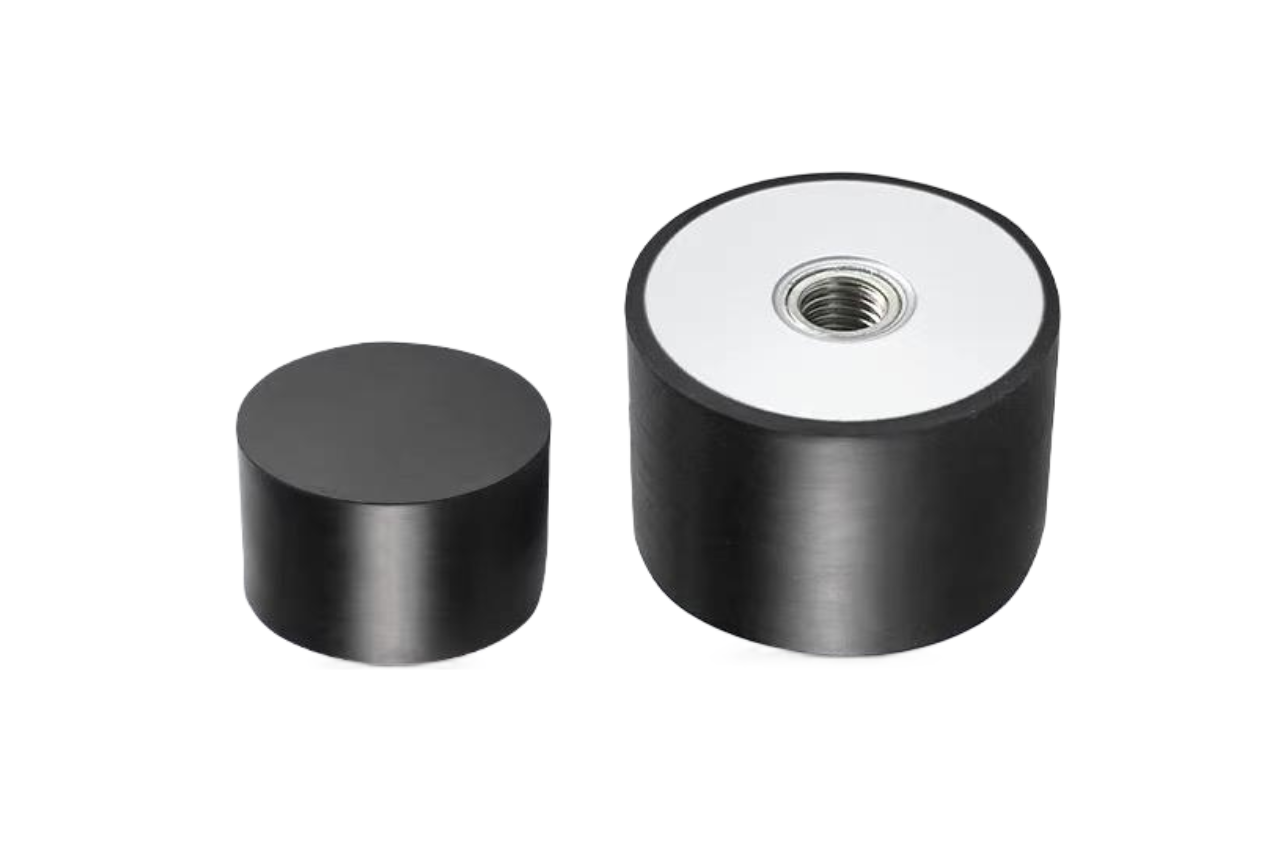
Cylindrical Mounts
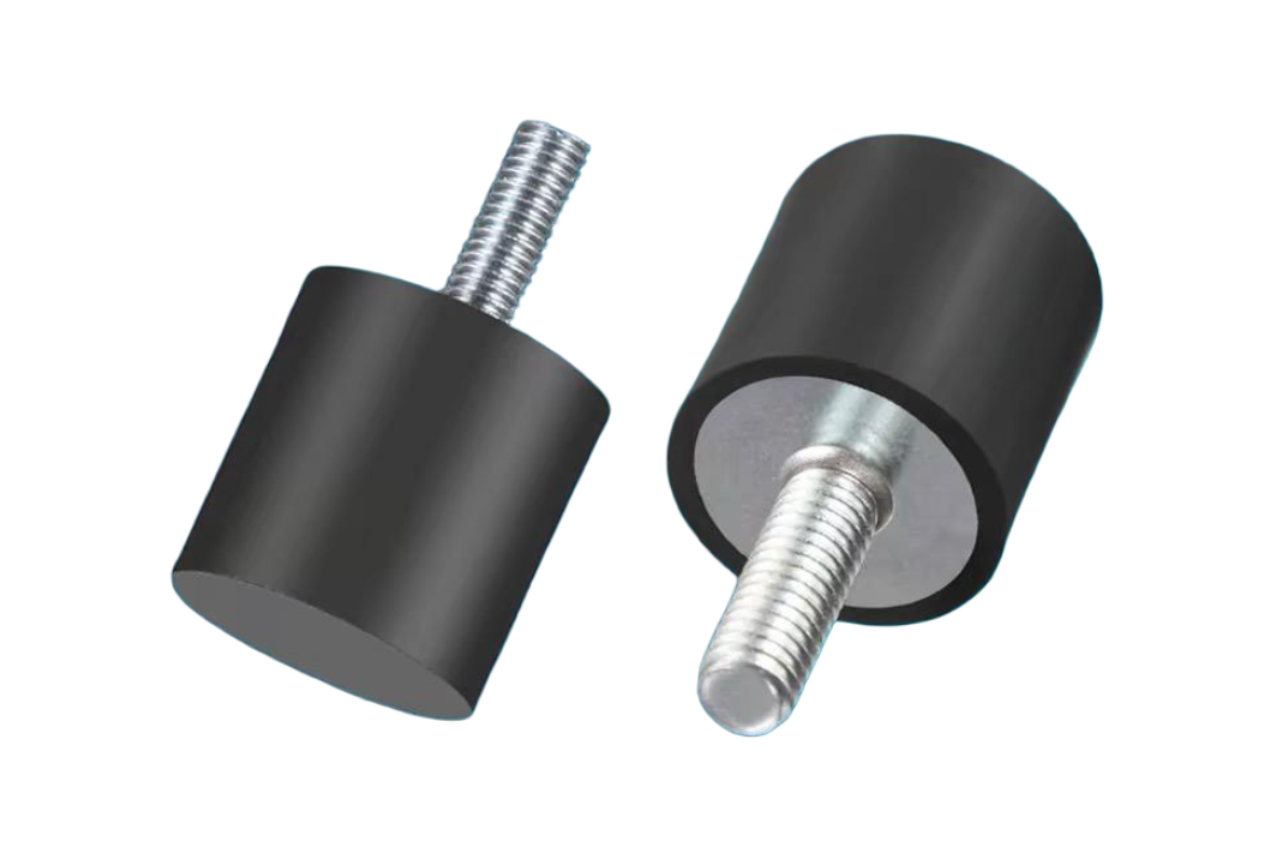
Cylindrical Mounts
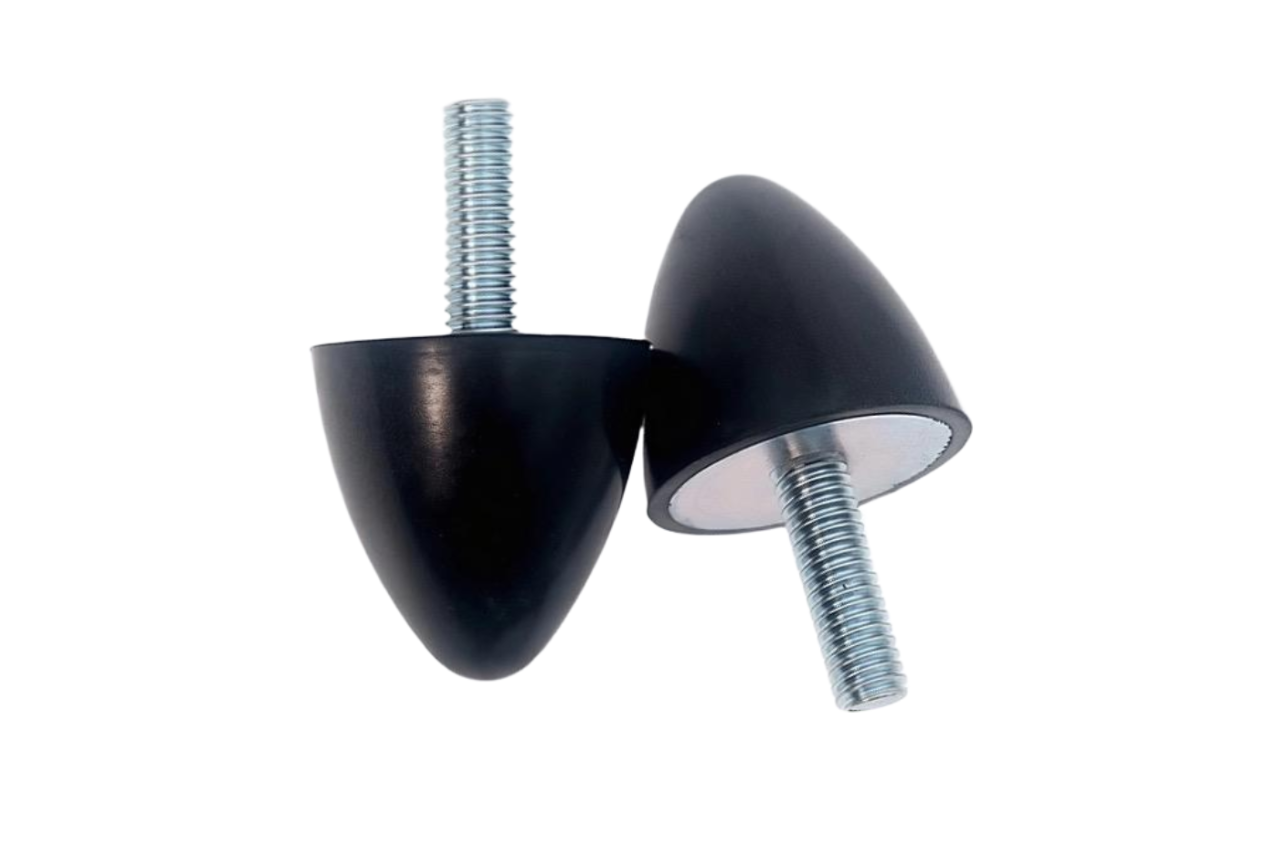
Rubber stop-damper
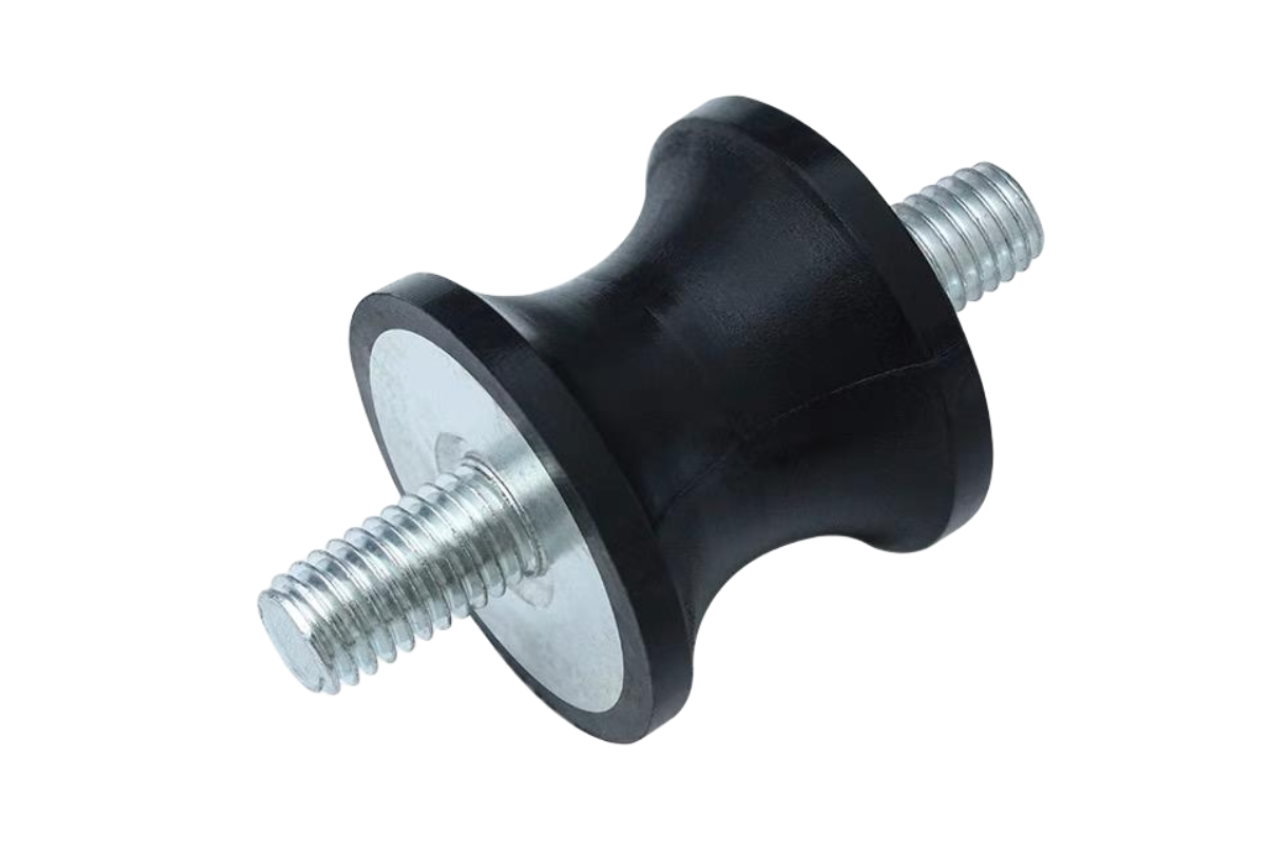
Rubber Isolator
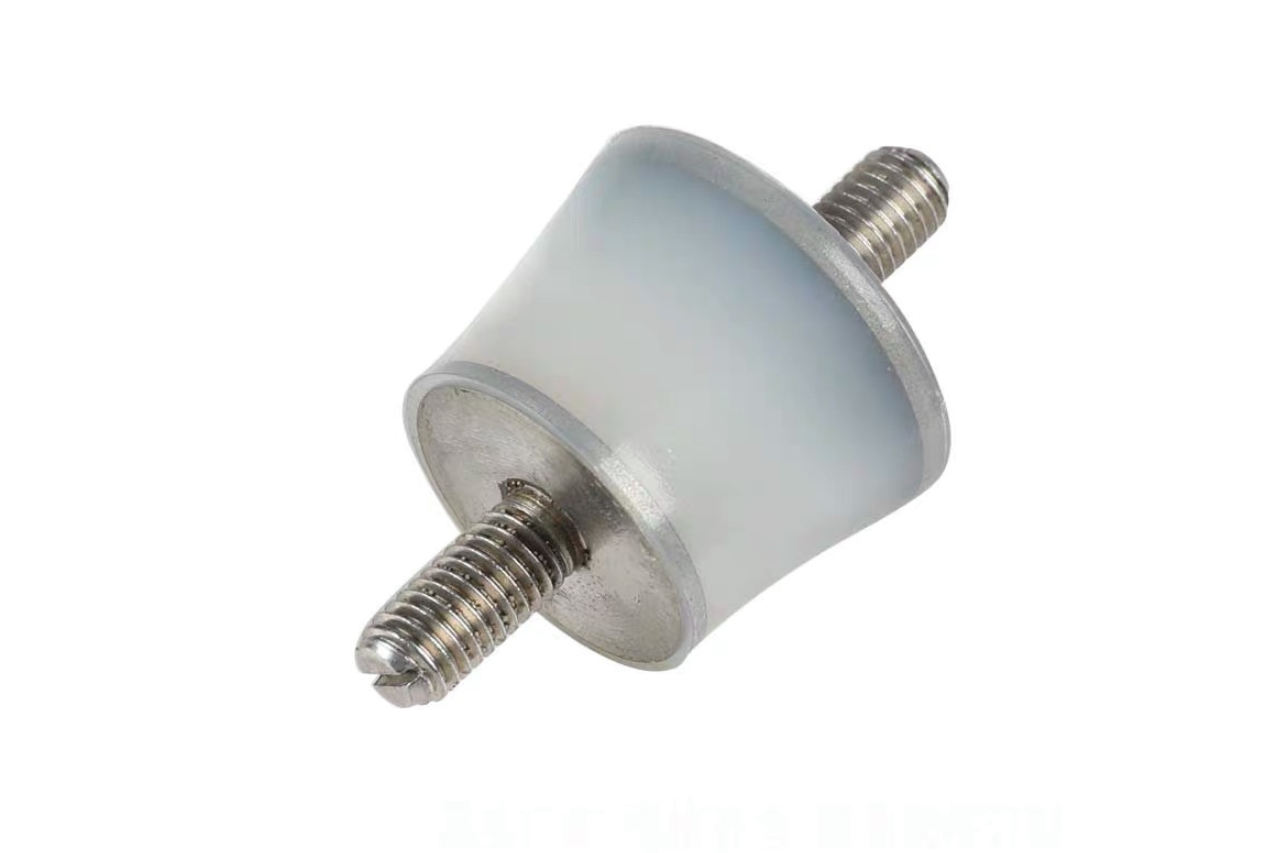
Cylindrical Mounts
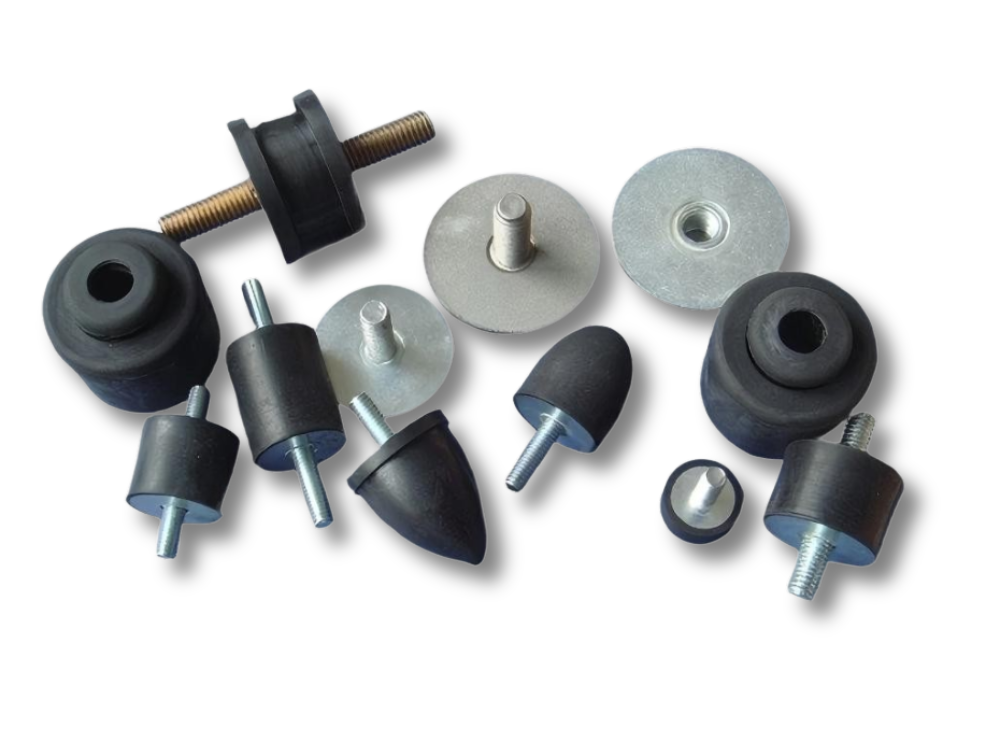
Rubber Cylindrical Mounts
Why Choose Us
Trusted Rubber Vibration Isolator Manufacturer with 30 Years of Expertise
Factory-direct solutions with natural rubber, customizable options, reliable quality, and trusted performance.
We own and operate our factory, ensuring strict quality control, stable lead times, and support for small-batch customization
With over three decades in vibration isolation, we offer trusted solutions backed by rich technical knowledge and real-world application.
Our isolators use pure natural rubber for excellent elasticity, durability, and superior shock absorption compared to synthetic materials.
Our ISO-compliant production lines and testing systems ensure consistent quality and reliable performance across all batches.
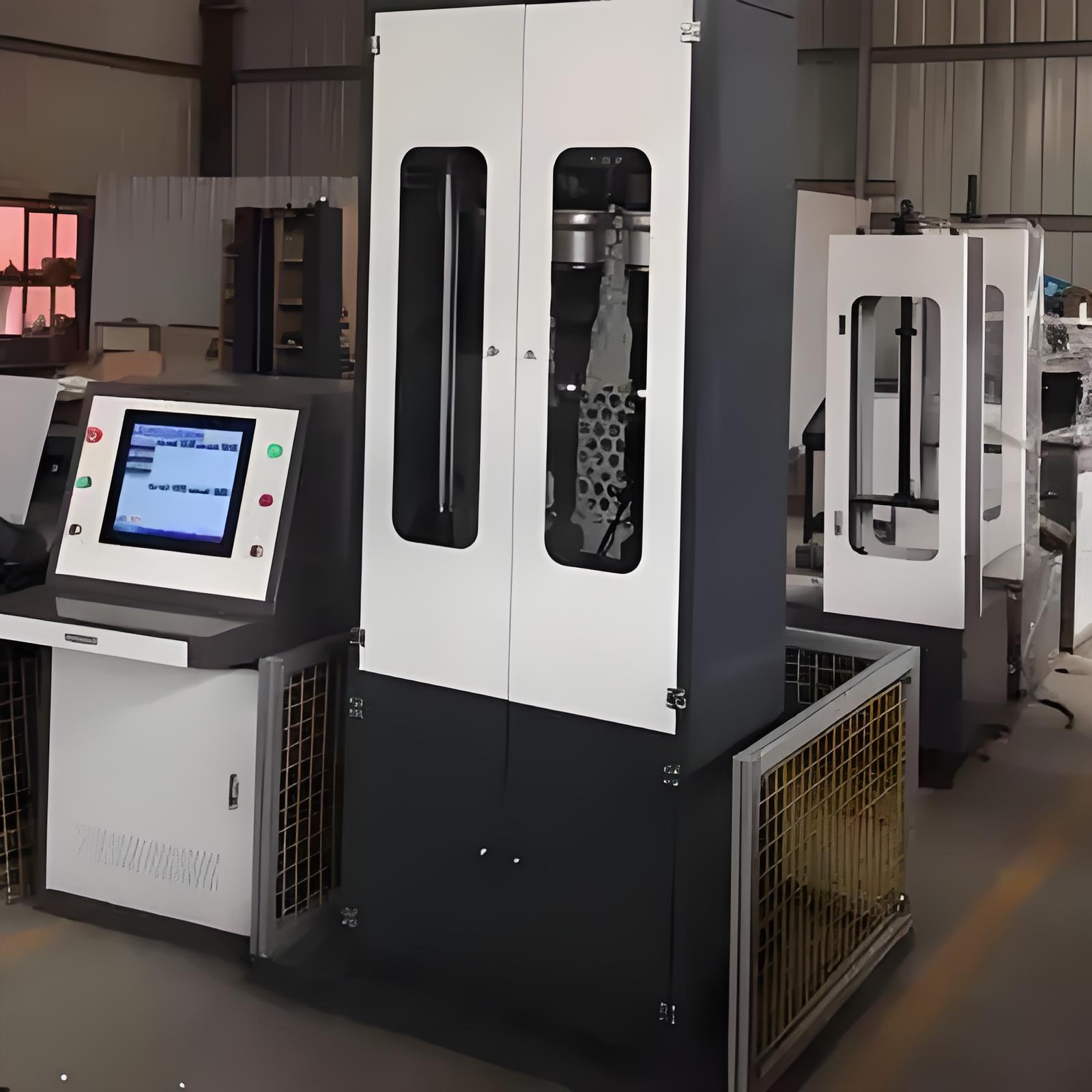
+86 13032112360
Common Questions
Most Popular Questions
1. Compression Mounting: Vertical Load Absorption
This mounting method is specifically designed for vertical vibrations, such as those caused by the weight of the equipment. The rubber isolator effectively absorbs vibrations through compression, making it suitable for applications like solar panels, rooftop units, and air conditioning systems.
2. Shear Mounting: Horizontal Damping Absorption
In this method, the rubber element absorbs shear forces applied horizontally. It is especially suitable for applications that generate lateral vibrations or motion during operation, such as fans, precision instruments, and equipment requiring enhanced lateral stability.
3. Combination Mounting (Compression + Shear): All-Around Vibration Isolation
This design allows the isolator to absorb both compressive and shear forces simultaneously, providing comprehensive multi-directional vibration isolation. It is ideal for complex operating environments where equipment is subjected to both vertical and horizontal vibrations, ensuring effective shock and vibration absorption.
4. Female Threaded Foot Mounting: Stable and Adjustable Installation
This type of base features an internal threaded design, allowing for quick and easy installation onto support structures. It is commonly used when isolators need to be mounted on a base, frame, or adjustable bracket. The installation is simple and suitable for medium to large equipment.
The size design of rubber cylindrical mounts directly impacts their vibration isolation effectiveness and application scope. Proper sizing ensures load capacity while influencing stiffness and frequency response, determining practical performance.
Relationship between diameter and height
The diameter and height define the support area and deformation ability. Larger diameters provide broader support to distribute loads; appropriate height allows sufficient deformation space for effective isolation.
Matching stiffness with size
Generally, larger sizes with thicker rubber layers have lower stiffness and better vibration isolation. However, too low stiffness can reduce load capacity. Balance between isolation and support is essential.
Frequency response characteristics
Size adjustments affect the mount’s natural frequency. Proper design avoids resonance with equipment operating frequencies, enhancing system stability.
Importance of custom sizing
Customizing mount sizes according to equipment load and installation space better meets performance requirements, overcoming limitations of standard models.
Conclusion
Scientific size design is crucial for effective vibration isolation and safe load bearing of rubber cylindrical mounts. Considering equipment characteristics and environment ensures optimal isolation performance.
Rubber durometer, commonly measured on the Shore A scale, plays a critical role in determining the performance characteristics of cylindrical rubber mounts. The durometer value directly affects stiffness, load capacity, vibration isolation efficiency, and the mount’s ability to endure dynamic stress.
Definition of durometer and Shore A rating
Durometer refers to the hardness of rubber and is typically measured using the Shore A scale. A lower Shore A rating (e.g., 30–40) means the rubber is softer and more flexible, while a higher rating (e.g., 70–80) indicates a firmer material.
How durometer affects vibration isolation
Softer rubber (low durometer):
Offers better vibration isolation at lower frequencies,
Allows greater deflection, absorbing more energy,
Is ideal for light equipment and noise-sensitive environments.
Harder rubber (high durometer):
Supports higher static and dynamic loads,
Provides better control at higher frequencies,
Is more suitable for heavy-duty machinery or tight space installations.
Impact on static and dynamic performance
Durometer influences both static compression and dynamic behavior:
Static: Lower durometer results in greater deformation under load, which helps in tuning the natural frequency of the system.
Dynamic: Softer mounts have higher internal damping but may degrade faster under cyclic stress. Harder mounts endure fatigue better but transmit more high-frequency vibration.
Application-specific selection
Choosing the right durometer depends on:
The weight of the mounted equipment,
The vibration frequency range,
The installation environment (temperature, chemicals, moisture),
The required service life and maintenance frequency.
Conclusion
Rubber durometer is one of the most important parameters when selecting a cylindrical mount. A proper balance between softness and rigidity ensures optimal vibration isolation, mechanical support, and durability. For custom performance, manufacturers often offer mounts in a range of Shore A hardness levels to suit different industrial needs.
The operating temperature range of rubber cylindrical mounts depends on the type of rubber material used. Different rubber compounds have varying temperature resistance properties. The most commonly used types include:
1. Natural Rubber
Operating Temperature Range: -40°F to 155°F (-40°C to 68°C)
Characteristics: Natural rubber offers excellent elasticity and impact resistance, making it suitable for standard temperature environments. It is typically used in applications that require moderate thermal stability.
2. Neoprene Rubber (Chloroprene)
Operating Temperature Range: 10°F to 180°F (-12°C to 82°C)
Characteristics: Neoprene rubber provides good weather and oil resistance, making it ideal for outdoor environments and applications exposed to chemicals. It is widely used in industries that deal with varying weather conditions or oily surfaces.
3. Nitrile Rubber (NBR)
Operating Temperature Range: -65°F to 300°F (-54°C to 149°C)
Characteristics: Nitrile rubber is known for its outstanding oil resistance, making it highly suitable for environments exposed to oils and chemicals. Its high-temperature tolerance makes it a preferred choice in automotive and petrochemical applications.
4. Silicone Rubber
Operating Temperature Range: -76°F to 446°F (-60°C to 230°C)
Characteristics: Silicone rubber is ideal for extremely high or low temperature environments. It is commonly used in medical devices, aerospace applications, and other industries that require high thermal stability and flexibility.
Conclusion
The specific operating temperature range of a rubber cylindrical mount varies depending on the type of rubber material selected. Choosing the right rubber compound according to the environmental temperature conditions is essential for ensuring performance, safety, and longevity.
Precision equipment such as medical instruments, laboratory devices, and sensitive measuring systems require an extremely stable environment to ensure accurate operation. Even slight vibrations can cause errors or damage delicate components. Controlling vibrations in such scenarios is challenging, and selecting the right vibration isolator is crucial.
Rubber cylindrical mounts, with their excellent vibration damping and shock absorption properties, can be an ideal solution for certain types of precision equipment—especially where moderate isolation and durability are needed.
Vibration Damping Characteristics of Rubber Cylindrical Mounts
Rubber cylindrical mounts are made of high-quality elastic rubber that deforms to absorb and dissipate vibration energy. This effectively reduces the amplitude and frequency of vibrations transmitted to the equipment, creating a quieter and more stable operating environment.
The cylindrical shape offers consistent support and mainly provides isolation in the vertical direction, which is especially important for instruments sensitive to vertical vibrations.
Applications in Precision Equipment
Rubber cylindrical mounts are well-suited for precision devices that operate within moderate vibration frequency ranges and do not require ultra-high isolation performance, such as:
Laboratory centrifuges
Analytical balances
Small medical imaging devices
Precision pumps and compressors
However, for extremely sensitive equipment that requires sub-micron vibration isolation, more specialized isolators—such as pneumatic or active isolation systems—may be necessary.
Advantages Over Other Isolation Methods
Compared to rigid mounts or basic rubber pads, rubber cylindrical mounts offer superior shock absorption and vibration damping due to their material and shape. Key advantages include:
Reliable vertical-axis vibration isolation
Resistance to environmental factors like moisture and temperature changes
Long service life with low maintenance requirements
These qualities make rubber cylindrical mounts a practical and economical choice for many types of precision instruments.
Installation and Maintenance Tips
Ensure proper mount selection based on the equipment’s weight and vibration profile.
Distribute mounts evenly to maintain balance.
Regularly inspect the rubber for signs of aging or cracking.
Avoid over-compression beyond the recommended load range.
Limitations
While rubber cylindrical mounts effectively reduce vibrations, they are passive isolators and cannot adapt to varying frequencies or amplitudes. For ultra-sensitive equipment operating in extremely low-vibration environments, advanced active isolation systems may be required.
Conclusion
Rubber cylindrical mounts are a highly effective solution for reducing vibration in various types of precision equipment. They help ensure stable operation and protect delicate components. With reliable vertical vibration isolation, durability, and easy installation, they are a popular choice for laboratory and medical devices that require moderate vibration control.
Rubber cylindrical mounts are widely used in industrial and mechanical systems to isolate vibration and absorb shock. However, their performance under static loads versus dynamic loads can differ significantly. Understanding this difference is crucial for selecting the right mount for your specific application, especially when dealing with equipment that experiences both constant and fluctuating forces.
Rubber mounts under static loads
Under static load conditions—such as the dead weight of a machine—rubber cylindrical mounts behave predictably. The rubber compresses to a certain extent based on:
The durometer (hardness) of the rubber,
The cross-sectional area and height of the mount,
And the magnitude of the static load.
This static compression is often used to calculate the natural frequency of the system. A properly loaded rubber mount will not be excessively compressed and will maintain its isolating function over time without material fatigue, assuming normal operating conditions.
Performance under dynamic loads
Dynamic loads involve fluctuating forces caused by equipment vibration, movement, or operational cycles. In such cases, rubber mounts:
Absorb energy through internal friction (hysteresis),
React with non-linear stiffness, especially at high strain rates,
Are affected by frequency-dependent damping properties.
Unlike static loading, dynamic loading introduces fatigue as a critical factor. Over time, cyclic stress may cause:
Cracking in the rubber surface,
Bond failure between rubber and metal,
Loss of elasticity and damping efficiency.
Material behavior and selection
Choosing the right rubber compound (e.g., natural rubber, neoprene, EPDM) is essential, as different materials offer different performance under cyclic or shock loads. In dynamic applications, materials with higher damping capabilities are often preferred to prevent resonance and extend mount life.
Design considerations
When selecting rubber cylindrical mounts for systems with both static and dynamic loads, it’s important to:
Match the static deflection to ensure proper frequency isolation,
Ensure the mount is within the dynamic fatigue threshold,
Consider temperature effects that may alter rubber behavior under load.
Conclusion
Rubber cylindrical mounts are excellent vibration isolators, but their effectiveness depends on how well they’re matched to the type of load they will carry. Static and dynamic loads influence mount behavior differently, and overlooking these distinctions can lead to premature wear or system failure. A careful balance of material choice, deflection analysis, and fatigue resistance ensures reliable and long-term performance.
The vibration characteristics of a mechanical system—particularly frequency and amplitude—are key factors when selecting rubber cylindrical mounts. These two parameters significantly influence a mount's isolation efficiency, service life, and performance under dynamic conditions.
Understanding frequency and amplitude
Frequency refers to how often the vibration occurs (measured in Hz). Low-frequency vibrations (e.g., <10 Hz) come from slow-rotating machines, while high-frequency vibrations (>100 Hz) may result from precision motors or gear mechanisms.
Amplitude refers to the magnitude or intensity of the vibration—the greater the amplitude, the more energy the system needs to absorb or isolate.
Impact of frequency on mount performance
The isolation effectiveness of a rubber mount is closely linked to the resonant frequency of the mount-system combination. To achieve optimal isolation:
The mount’s natural frequency should be well below the operating vibration frequency.
Lower-frequency applications require softer rubber with more deflection.
Higher-frequency environments may benefit from firmer materials that resist excessive motion but still isolate some vibration.
Influence of amplitude on material selection
Larger vibration amplitudes can overstress rubber mounts if not properly rated. As amplitude increases:
The mount must have adequate displacement capacity without bottoming out.
Rubber compounds must be selected for high dynamic strain tolerance.
Designs may need higher vertical deflection or progressive stiffness profiles to manage energy effectively.
Dynamic performance and fatigue
High-frequency, high-amplitude vibrations accelerate fatigue in rubber:
Frequent cycling causes internal heat build-up, leading to material degradation.
Long-term exposure to combined high frequency and amplitude can cause cracks, bond failures, or compression set.
Engineering considerations
To match a mount to frequency and amplitude:
Perform a vibration analysis on the equipment to determine input spectra.
Choose mounts with suitable static deflection, resonant frequency, and material damping.
Consider using finite element analysis (FEA) or consult manufacturers for precision applications.
Conclusion
Frequency and amplitude are not just technical details—they define the dynamic behavior your rubber mount must withstand. A mismatch can result in inadequate isolation, premature failure, and even equipment damage. Proper mount selection ensures performance, safety, and longevity in vibration-prone systems.
The shape of a rubber mount plays a crucial role in how loads and stresses are distributed during operation. The cylindrical design is one of the most widely used geometries in vibration isolation due to its unique mechanical advantages in compression strength, multi-directional stability, and stress distribution.
Mechanical characteristics of cylindrical mounts
The symmetrical geometry of cylinders ensures uniform stress distribution under axial loads. This helps maintain structural integrity, minimizes local fatigue, and reduces the risk of tearing or rubber failure during extended use.
Load distribution benefits
Axial load balance: Cylindrical mounts effectively distribute vertical loads evenly, reducing the risk of bottoming out or uneven compression.
Off-center load tolerance: Compared to square or irregular shapes, cylindrical mounts better accommodate side loads or misalignment without compromising performance.
Radial support: They also offer effective support and flexibility in the radial direction, making them suitable for dynamic systems with unpredictable vibration directions.
Performance under multi-directional vibration
Thanks to their symmetrical structure, cylindrical rubber mounts exhibit consistent stiffness and damping characteristics in multiple directions. This makes them ideal for equipment experiencing multi-axis motion, such as:
HVAC compressors
Diesel generators
Air-cooled condenser units
Impact on fatigue life
The even load distribution in cylindrical mounts reduces internal heat buildup and stress concentration, leading to longer fatigue life and less frequent replacements. This improves cost-efficiency in long-term operation.
Conclusion
Cylindrical rubber mounts are not only structurally simple but also mechanically efficient. Their ability to distribute loads evenly and respond to multi-directional vibration makes them an excellent choice for industrial vibration control applications.
Rubber cylindrical mounts may experience various failure modes during their service life, which can compromise vibration isolation performance and lead to safety risks and economic losses. Understanding common failure types and their causes is essential for implementing effective prevention strategies and extending mount longevity.
Common failure modes
Rubber aging and hardening
Exposure to UV radiation, ozone, high temperatures, and chemicals causes rubber to age, harden, crack, and eventually lose elasticity and isolation properties.Fatigue cracking
Repeated dynamic loading causes stress concentration zones within the mount to develop micro-cracks that propagate over time, leading to material failure.Permanent compression set
Under sustained static or cyclic loads, rubber may undergo irreversible deformation, reducing mount height and diminishing isolation efficiency.Bond failure
Many mounts rely on adhesive bonding between rubber and metal parts. Vibration and environmental exposure can degrade this bond, weakening structural integrity.
Prevention strategies
Use high-quality rubber compounds such as natural rubber or neoprene with superior aging resistance.
Design and install mounts to avoid overload and uneven loading, ensuring operation within specifications.
Conduct regular inspections and maintenance to detect surface cracks, deformation, or bond issues early.
Implement environmental protection such as shielding from sunlight, dust, and chemical exposure.
Ensure proper storage away from heat, direct sunlight, and humidity.
Conclusion
Knowing the failure mechanisms and prevention measures for rubber cylindrical mounts is vital for stable equipment operation and cost-effective maintenance. With proper material selection, design, and upkeep, the service life of mounts can be significantly extended, enhancing system reliability.
1.Load and Direction: Understand the Static and Dynamic Loads on Your Mount
When selecting a vibration isolator, it's essential to understand the static and dynamic loads the mount will bear. Static loads refer to the weight of the equipment, while dynamic loads come from vibrations, shocks, or movements during operation. Identifying these load types helps ensure that the appropriate isolator is chosen to maintain smooth equipment performance and minimize long-term vibration damage.
2.Vibration Frequency: Ensure the Natural Frequency of the Mount Avoids Equipment Resonance
Every isolator has its own natural frequency. If the mount’s natural frequency aligns with the operating frequency of the equipment, resonance may occur, leading to excessive vibrations. When selecting an isolator, make sure its natural frequency is well separated from the equipment’s operating frequency to reduce the risk of damage and ensure long-term stability.
3.Installation Space and Thread Type: Choose the Right Size and Thread Configuration
Select an isolator size that fits within the available installation space. Additionally, isolators come with different thread types—such as male (external) or female (internal) threads. Choosing the correct thread type ensures quick and secure connection between the isolator and the equipment or support structure, improving both support and stability.
4.Environmental Conditions: Consider Temperature, Humidity, and Chemical Exposure
Environmental factors must be considered when selecting a vibration isolator. Conditions such as temperature extremes, humidity, and exposure to chemicals can affect the performance of the isolator material. For instance, extreme temperatures can impact rubber elasticity, and chemical exposure may cause corrosion. Choosing materials and mounts designed for specific environmental conditions ensures longer service life and operational reliability.
Rubber cylindrical mounts are widely used in various machinery due to their excellent vibration isolation and compact design, enhancing equipment stability and longevity. This article introduces typical application scenarios.
Generator set vibration isolation
Generators produce strong vibrations during operation; installing rubber cylindrical mounts effectively isolates vibration, reducing impacts on foundations and structures.
Pump equipment vibration control
Pump vibrations transmit through pipelines and supports; mounts absorb vibration energy, preventing resonance damage to equipment and piping.
Applications in HVAC systems
HVAC units and fans generate significant vibration; using cylindrical mounts reduces noise and vibration, improving indoor environmental quality.
Vibration protection for precision instruments
Mounts isolate environmental vibrations in precision instruments and testing equipment, ensuring measurement accuracy and stable operation.
Industrial automation equipment
Automation lines use mounts on robotic arms and conveyors to reduce vibration interference, enhancing production efficiency and product quality.
Conclusion
Rubber cylindrical mounts are versatile and suitable for many devices and industries. Effective vibration isolation improves equipment performance and lifespan, making them vital components in industrial vibration solutions.
The load capacity of rubber cylindrical mounts is one of the key performance indicators. Properly matching the mount's load capacity with the actual equipment requirements ensures stable operation, optimal vibration isolation, and prevents failures caused by overload or insufficient support.
Definition of load capacity
Load capacity refers to the maximum static or dynamic load a mount can withstand without permanent deformation or structural damage. This metric is crucial for bearing equipment weight and vibration impacts.
Impact of load capacity on stiffness
Generally, as load capacity increases, the mount’s stiffness also rises. Higher stiffness reduces deformation under heavy loads, supporting equipment stability. However, excessive stiffness can decrease vibration isolation effectiveness, especially for low-frequency vibrations. Conversely, lower stiffness improves isolation but may cause insufficient support, leading to rubber deformation and damage.
Load capacity and service life relationship
Operating mounts beyond their load capacity subjects rubber to greater stress, accelerating fatigue and permanent deformation, thus significantly shortening service life. Overloading can also worsen equipment vibration, affecting stability and safety. Proper load design extends mount lifespan and reduces maintenance costs.
How to select suitable load capacity
When selecting rubber cylindrical mounts, consider equipment weight, vibration frequency, amplitude, and operating environment to calculate appropriate load capacity. Excessive or insufficient load negatively impacts isolation performance and equipment safety. It is advisable to include a safety margin for occasional shock loads.
Conclusion
Load capacity is a core parameter influencing the performance of rubber cylindrical mounts. Scientific and reasonable load matching ensures stable mount operation and significantly improves isolation effectiveness and equipment reliability. Users should choose the most suitable load capacity based on specific working conditions to achieve long-term safe equipment operation.