Rubber Bell Mounts
Engineered to Protect Machinery in Demanding Environments
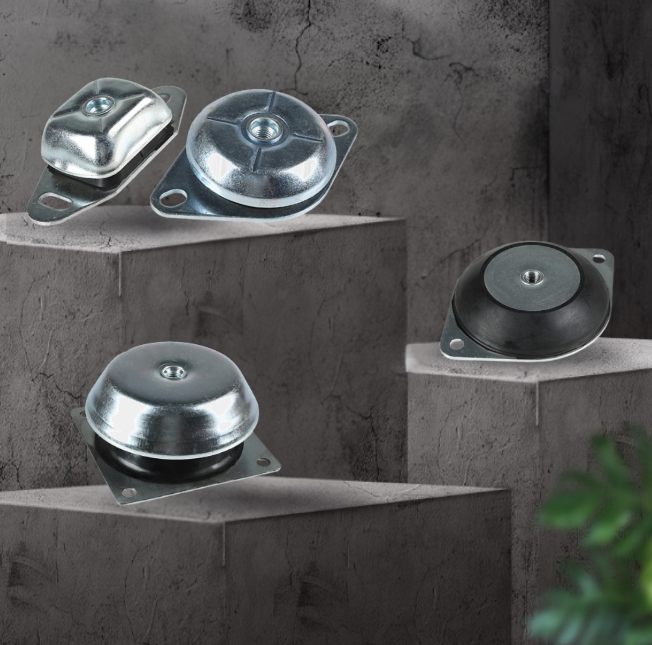
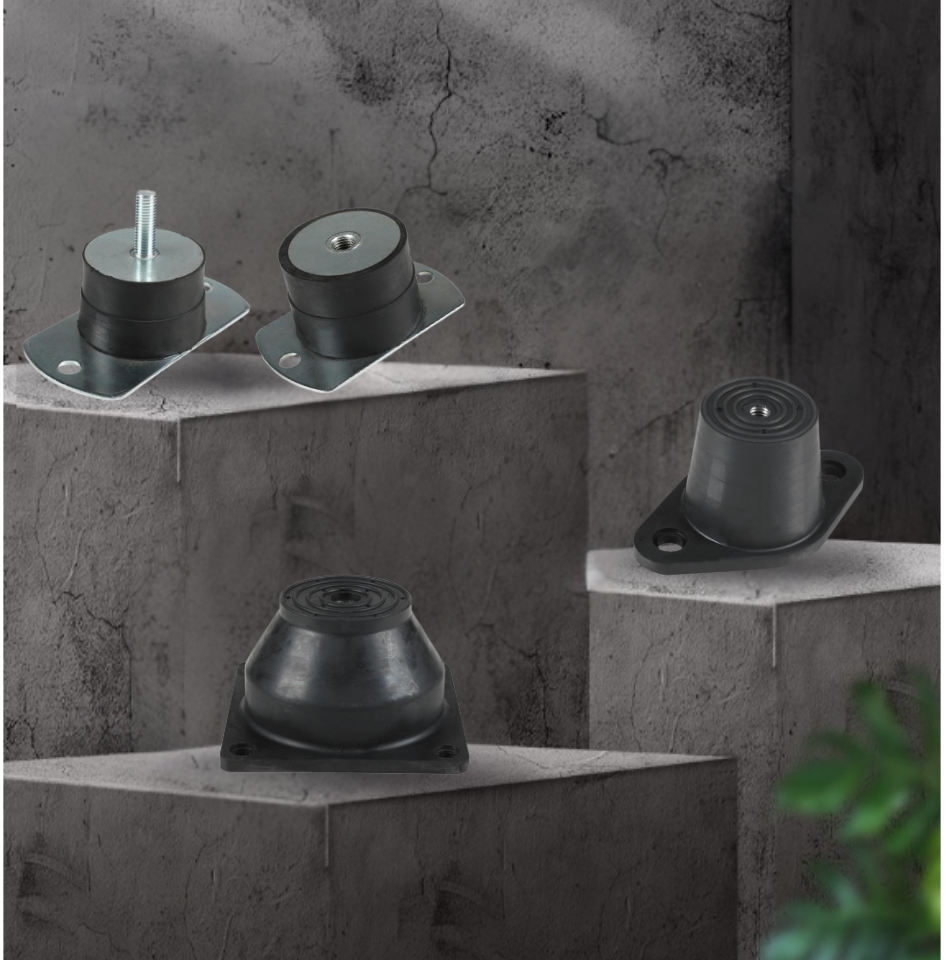
Our products
Rubber Bell Mounts
- FRH/FRS Bell Mounts
- FRHQ/FRSQ Bell Mounts
- MARINE Bell Mounts
- VBL Series Bell Mounts
- DBL Series Bell Mounts
- RM Series Bell Mounts
- PDRS Series Bell Mounts
- PSP Series Bell Mounts
Product Showcase
Bell Mounts: Reliable Vibration Isolation for Sensitive Equipment
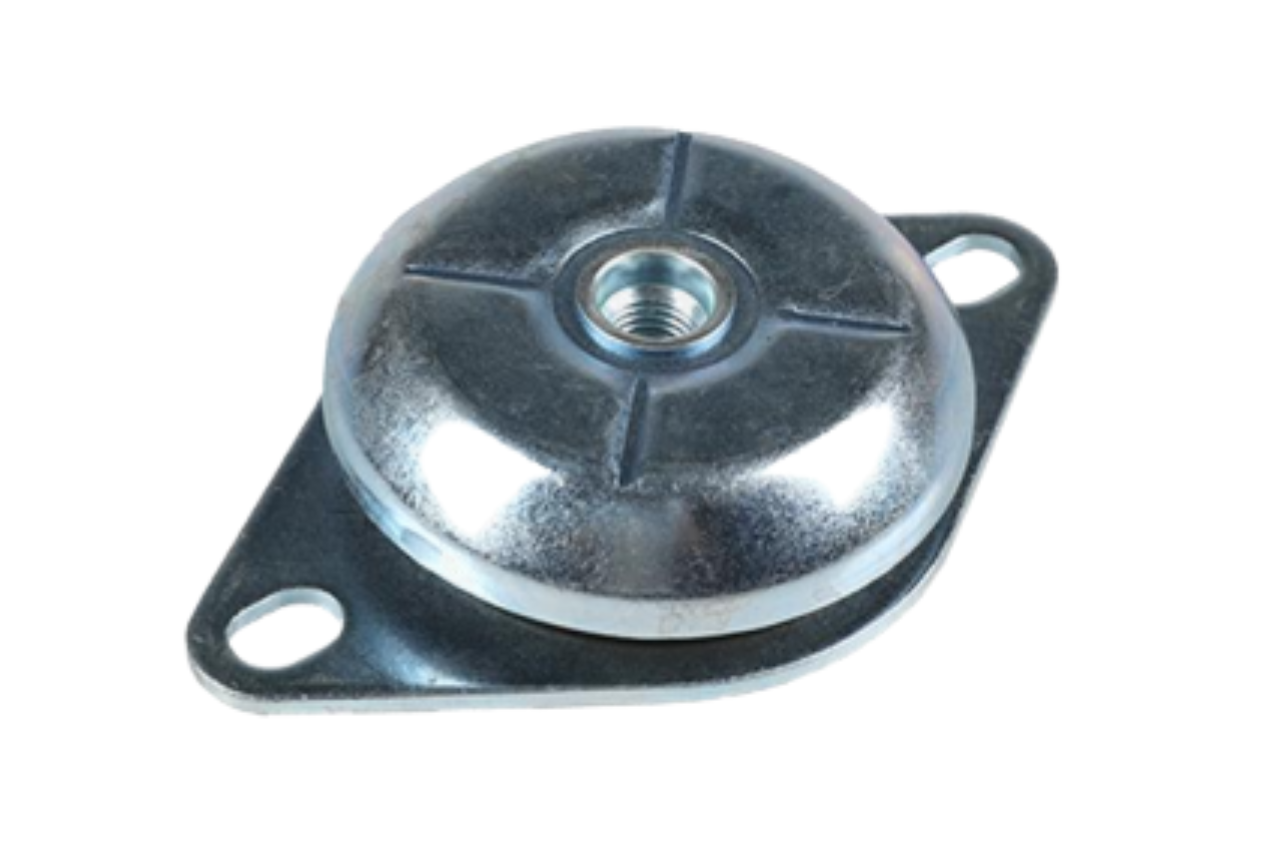
Rubber Bell Mounts
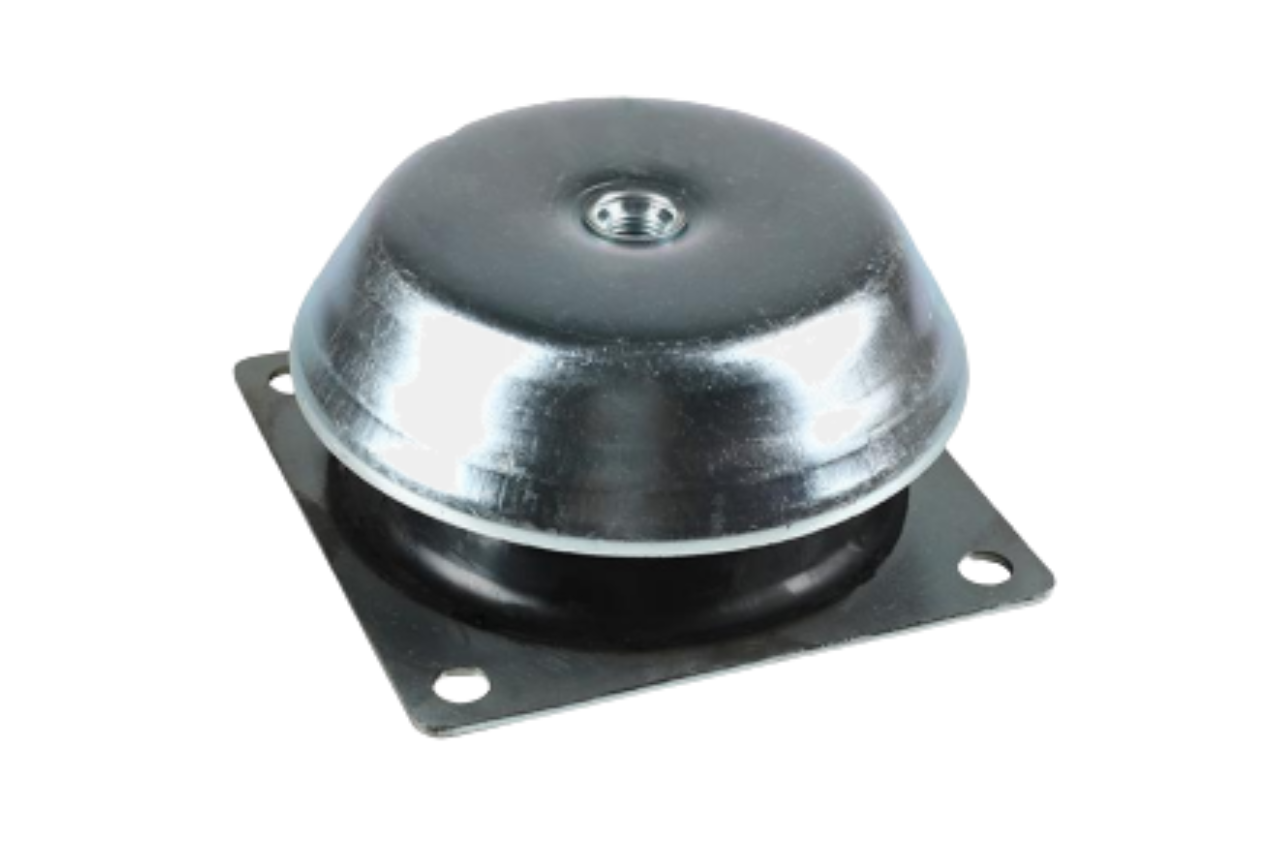
Rubber Bell Mounts
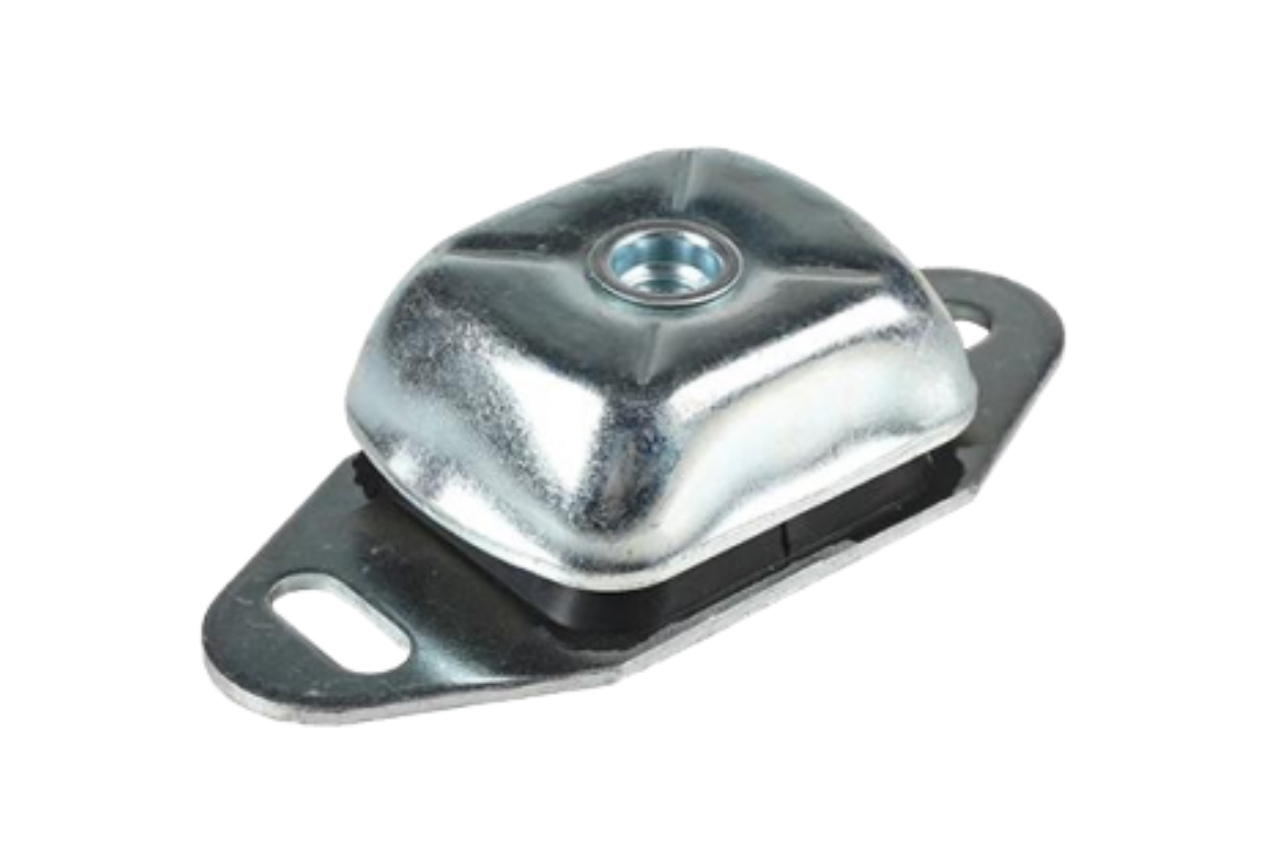
Rubber Bell Mounts
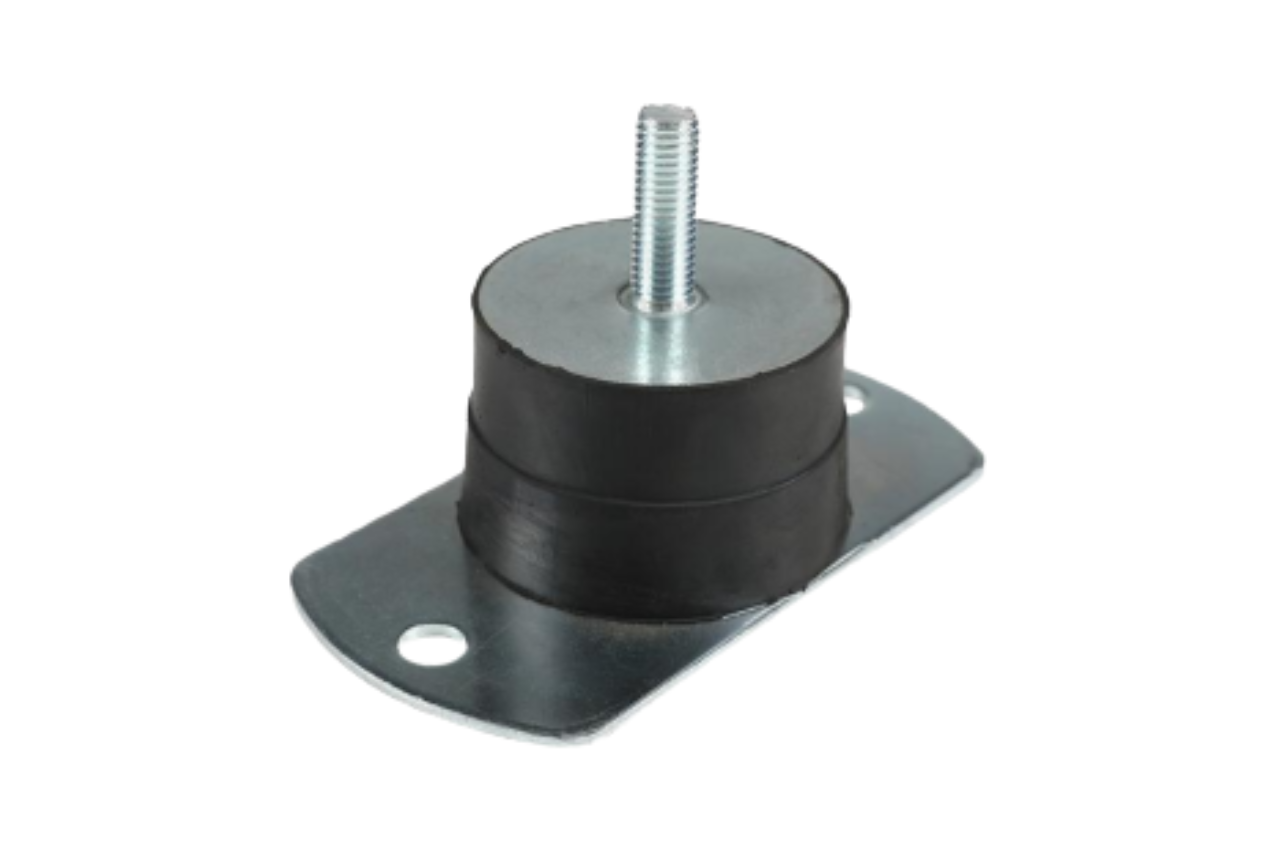
Rubber Bell Mounts
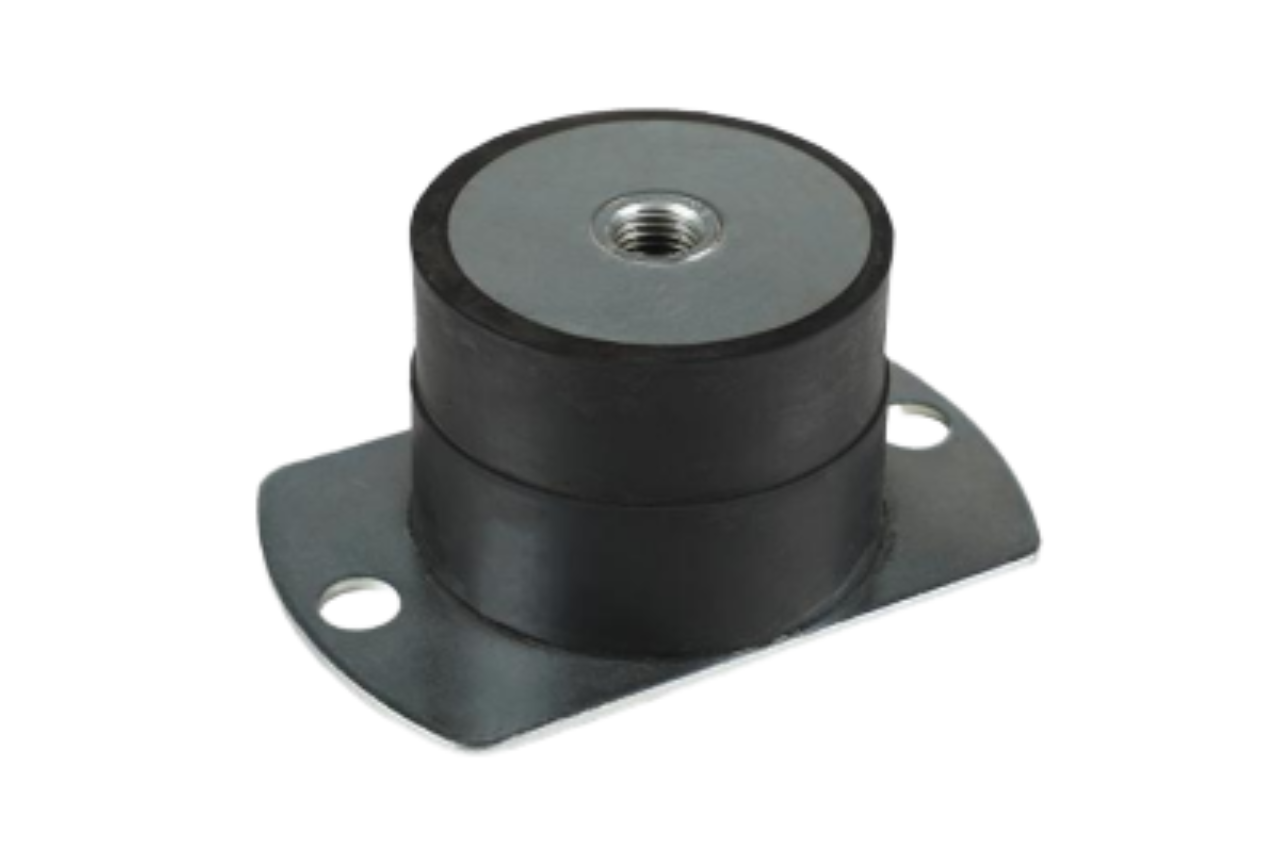
Rubber Bell Mounts
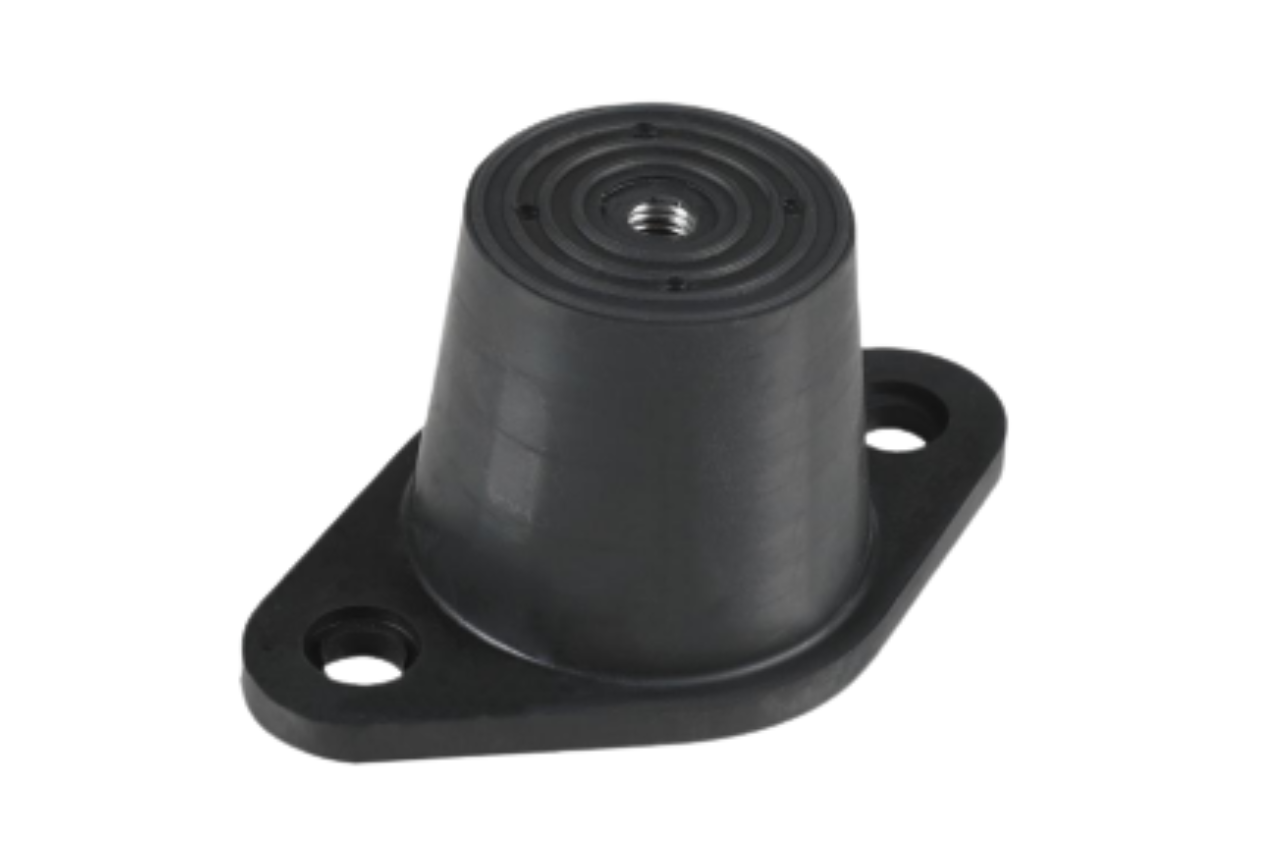
Rubber Bell Mounts
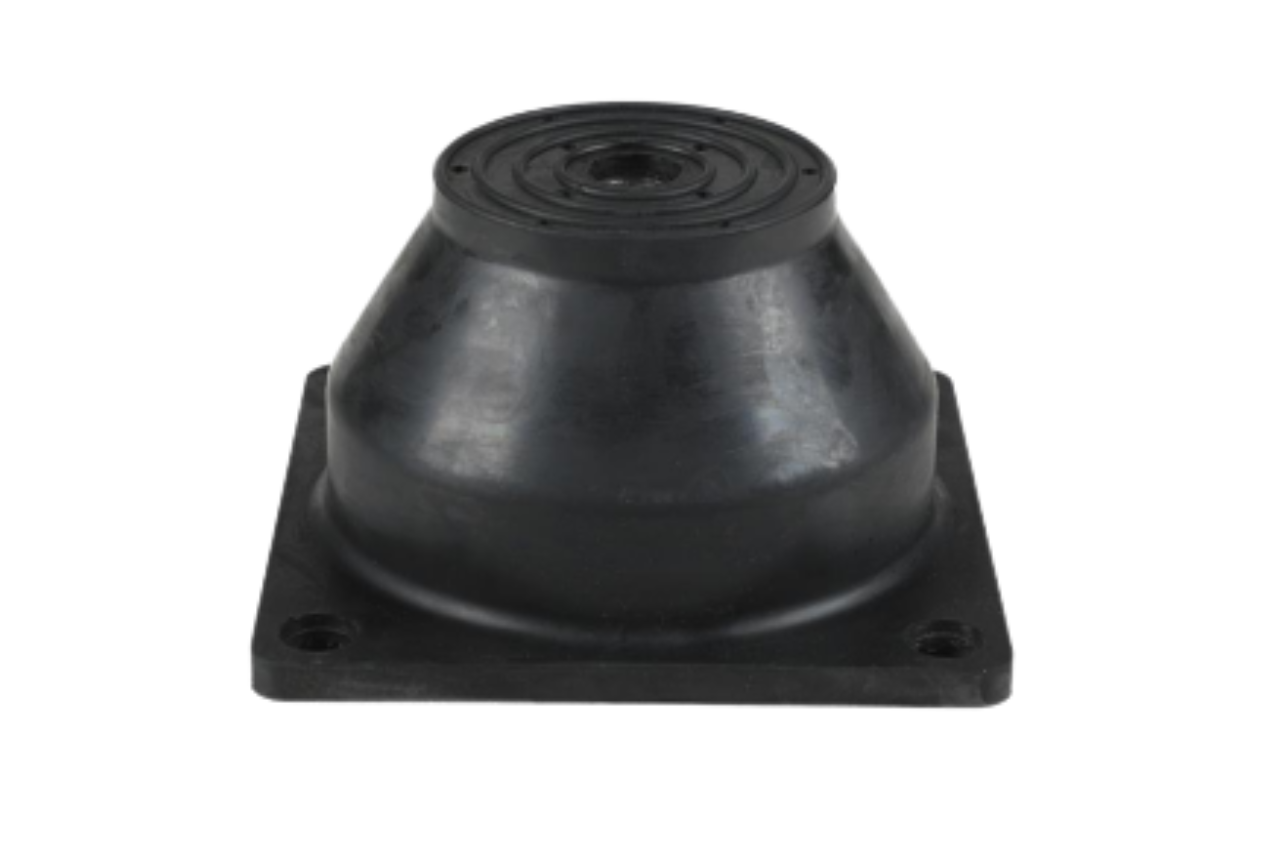
Rubber Bell Mounts
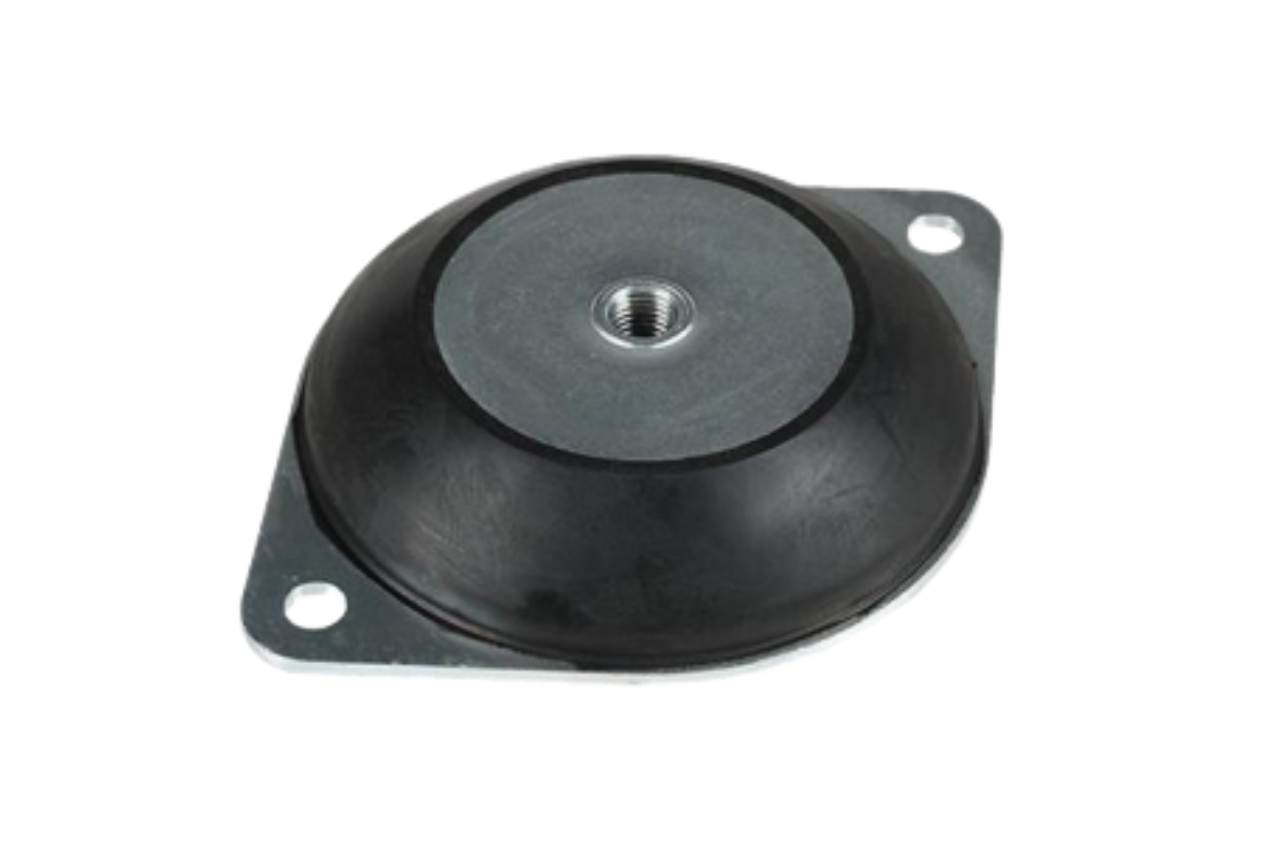
Rubber Bell Mounts
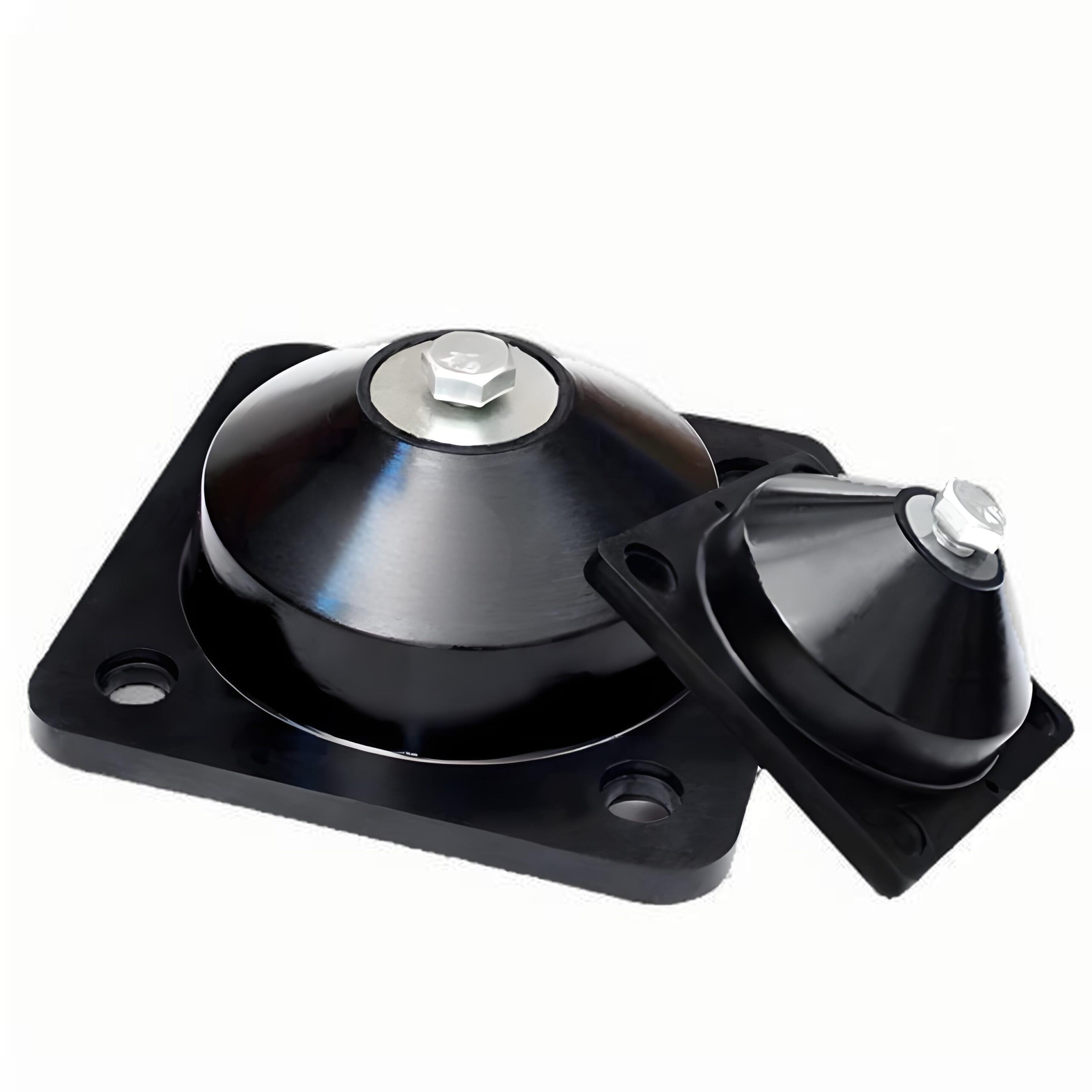
Rubber Bell Mounts
Why Choose Us
Trusted Rubber Vibration Isolator Manufacturer with 30 Years of Expertise
Factory-direct solutions with natural rubber, customizable options, reliable quality, and trusted performance.
We own and operate our factory, ensuring strict quality control, stable lead times, and support for small-batch customization
With over three decades in vibration isolation, we offer trusted solutions backed by rich technical knowledge and real-world application.
Our isolators use pure natural rubber for excellent elasticity, durability, and superior shock absorption compared to synthetic materials.
Our ISO-compliant production lines and testing systems ensure consistent quality and reliable performance across all batches.
+86 13032112360
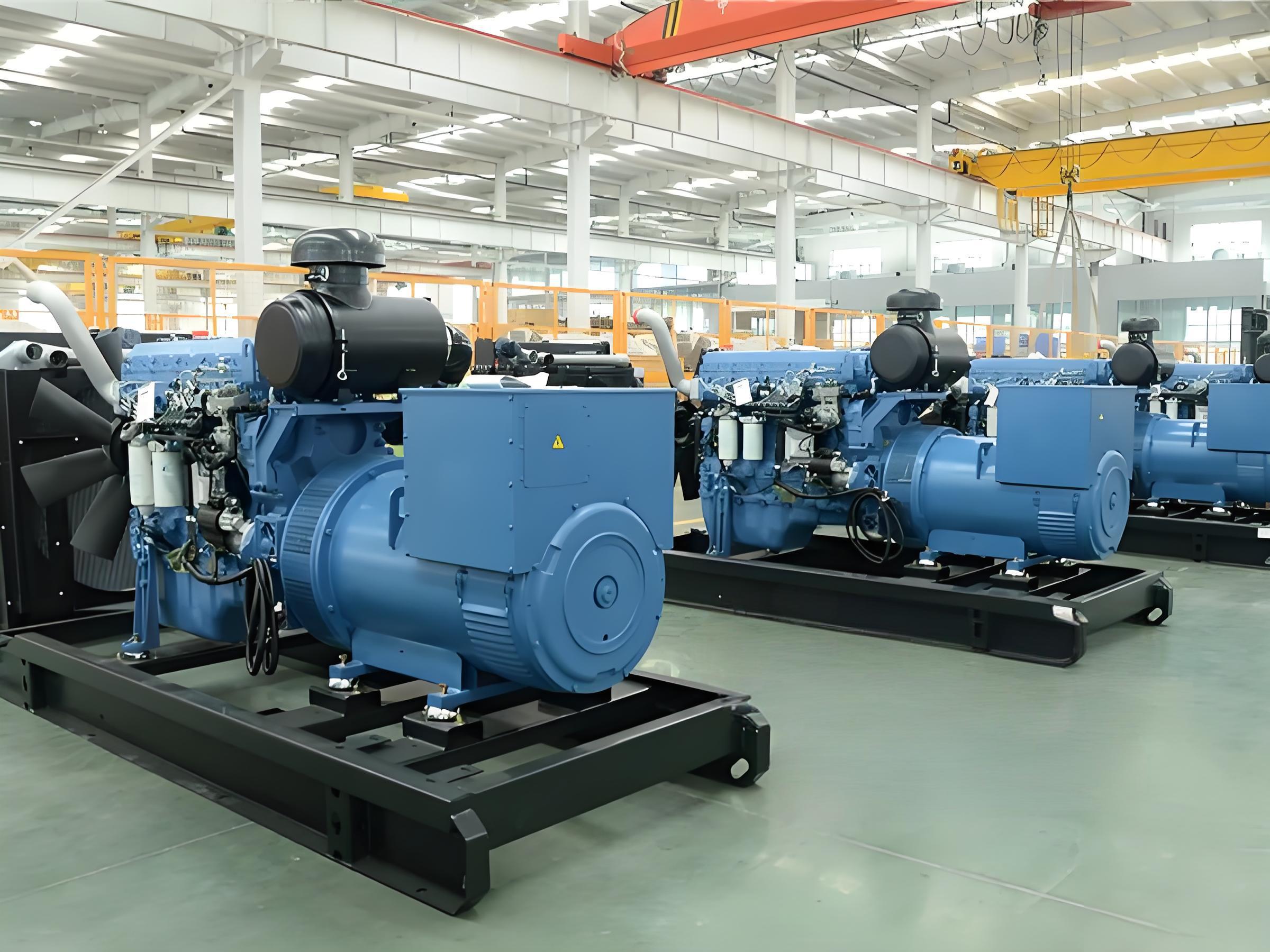
Common Questions
Most Popular Questions
A bell mount is a type of vibration isolator that features a distinctive bell-shaped metal housing paired with an internal rubber component. This design allows it to provide effective damping of vibrations and noise generated by mechanical equipment during operation. The bell shape is not just aesthetic—it serves both protective and structural purposes, shielding the rubber core and ensuring stable load distribution.
Bell mounts are commonly used in machinery where space is limited and moderate to high vibration damping is needed. This includes HVAC systems, water pumps, compressors, and generators. Their design combines the elasticity of rubber with the strength of metal, offering a compact solution that performs reliably across various industrial environments.
The primary function of a bell mount is to reduce transmission of vibrational energy from equipment to its mounting base, thereby protecting both the equipment and the structure. By minimizing noise and vibration, bell mounts help extend the lifespan of components, improve working conditions, and ensure smoother machinery operation.
Manufacturers such as Songjiangflex often provide custom bell mounts with various rubber hardness levels (Shore A), sizes, and load-bearing capacities to meet the specific needs of each application. Whether it's for rooftop AHUs or diesel generators on marine vessels, bell mounts offer a well-balanced solution for vibration control.
Bell mounts are widely used across various industries where vibration and noise control are critical to equipment performance and structural safety. Their compact design and efficient damping capability make them a popular choice for both light-duty and heavy-duty applications.
One of the most common areas where bell mounts are applied is the HVAC industry. They are frequently installed in air handling units (AHUs) and fan coil units (FCUs) to reduce the vibration transmitted to building structures. This not only improves system efficiency but also minimizes operational noise in indoor environments such as hotels, offices, and hospitals.
Bell mounts are also highly effective in pump and compressor systems. These machines generate significant mechanical vibrations during operation. Using bell mounts helps isolate these vibrations, reducing wear on the equipment and lowering the risk of structural damage.
In diesel generator sets, bell mounts serve as essential anti-vibration supports. They absorb the engine’s dynamic forces, ensuring smooth operation and protecting the mounting base from stress and fatigue. This is especially important in emergency power systems where reliability is critical.
Marine and offshore applications also benefit from bell mounts. Due to their corrosion-resistant construction and compact profile, bell mounts are ideal for use in ship engines, hydraulic systems, and onboard HVAC systems, where space and environmental resistance are both important.
In summary, bell mounts are used in:
- HVAC equipment (AHU, FCU)
- Water pumps and compressors
- Diesel and gas generators
- Marine vessels and offshore rigs
- Industrial machinery and power units
Wherever vibration and structure-borne noise need to be minimized, bell mounts offer a durable and space-saving solution.
Rooftop equipment such as cooling towers, air handling units (AHUs), and generators often produce significant vibration. These vibrations can travel through concrete structures, disturbing building occupants and, over time, leading to fatigue or micro-cracks in roof slabs. Without proper isolation, the roof becomes a channel for structural noise and vibration.
Rubber bell mounts effectively isolate the equipment from the building structure, significantly reducing vibration transmission to concrete roofs. Their flexible, bell-shaped design absorbs and attenuates vibration energy, preventing structural noise propagation and protecting rooftop integrity. They are ideal for HVAC systems, fans, and generators installed on rooftops.
How Bell Mounts Work
Bell mounts use specially molded rubber components that isolate vibrations in both vertical and horizontal directions. The bell-shaped form provides greater displacement capacity and energy absorption. When the equipment operates, the rubber body undergoes elastic deformation, effectively blocking the transmission of vibration into the concrete structure. This helps reduce structure-borne noise and extends the lifespan of both equipment and the rooftop.
Common Rooftop Applications
Rubber bell mounts are commonly used for:
Rooftop air handling systems (AHU, FCU)
Cooling towers in commercial buildings
Diesel generators on industrial rooftops
Rooftop electrical cabinets and solar inverters
With weather-resistant rubber, these mounts can withstand exposure to rain, UV, humidity, and temperature fluctuations for long-term outdoor use.
Installation Tips
To achieve optimal vibration isolation:
Select models based on equipment weight and vibration frequency
Install mounts symmetrically under the equipment
Use steel base plates if extra stability is needed
Avoid direct anchoring of equipment to concrete — use anchored isolation systems instead
When installed correctly, vibration transmission can be reduced by more than 80%.
Why Bell Mounts Perform Better than Flat Rubber Pads
Flat rubber pads offer basic isolation, but bell mounts provide key advantages:
Dual-direction (vertical + lateral) vibration isolation
Greater durability under dynamic loads
Better stability on uneven rooftop surfaces
Superior resistance to weathering and UV exposure
They are a more professional and long-lasting solution for rooftop vibration issues.
Conclusion
Yes, rubber bell mounts can significantly reduce vibration transmission from equipment to concrete roofs. Their unique rubber structure and excellent elastic properties make them a reliable choice for protecting rooftops, reducing noise, and ensuring smooth, quiet operation of rooftop machinery.
Compressors and pumps are essential equipment in many industrial and commercial settings, but they inherently produce vibrations during operation. These vibrations can cause noise, mechanical wear, and even damage to connected piping and foundations if not properly controlled.
Bell mounts offer a practical and effective solution to reduce these unwanted vibrations.
How Bell Mounts Work to Isolate Vibration
Bell mounts consist of a resilient rubber body shaped like a bell, often combined with metal inserts for stability. This design allows the mount to flex and absorb vibrational energy generated by compressors and pumps. When the equipment vibrates, the rubber compresses and deforms elastically, converting kinetic energy into heat and reducing the amount of vibration transmitted to the surrounding structure.
Benefits of Using Bell Mounts for Pumps and Compressors
Dampening Multiple Directions: Bell mounts isolate vibration in vertical and horizontal directions, which is crucial because pumps and compressors often vibrate in complex patterns.
Reducing Noise: By minimizing vibration transmission, bell mounts also reduce structure-borne noise that can travel through floors and walls.
Protecting Equipment and Infrastructure: Reduced vibration lowers wear on equipment parts and connected piping, extending service life and reducing maintenance costs.
Easy Installation: Bell mounts are compact and simple to install under existing equipment bases without major modifications.
Typical Applications
HVAC compressors in commercial buildings
Water pumps in industrial plants
Refrigeration compressors in supermarkets and cold storage
Air compressors in manufacturing facilities
Their durability and weather resistance also make bell mounts suitable for outdoor or rooftop installations.
Installation Considerations
For optimal vibration isolation:
Choose bell mounts sized for the weight and vibration frequency of the equipment.
Position mounts evenly under the equipment base to distribute load.
Avoid rigid connections between equipment and structure; the mounts should provide a flexible interface.
Periodically inspect mounts for wear or degradation and replace when necessary.
Why Bell Mounts Are Preferred Over Other Isolators
Compared to flat pads or coil springs, bell mounts offer a balanced combination of flexibility, load capacity, and durability. Their molded rubber design provides inherent damping without the need for additional components. This makes them highly effective and low maintenance.
Conclusion
Bell mounts reduce compressor and pump vibration by absorbing and isolating vibrational energy through their flexible rubber bell shape. This not only improves equipment longevity and reduces noise but also protects building structures. Their ease of installation and proven effectiveness make them a popular choice for vibration control in a wide range of applications.
Yes — bell mounts are exceptionally well-suited for HVAC systems. In fact, they are among the most commonly used vibration isolators in heating, ventilation, and air conditioning (HVAC) applications due to their compact size, effective vibration control, and durability in challenging environments.
1. Why HVAC Systems Need Vibration Isolation
HVAC equipment such as AHUs (Air Handling Units), FCUs (Fan Coil Units), compressors, and chillers all produce mechanical vibrations during operation. These vibrations can:
Transfer to building structures
Cause disturbing noise
Lead to premature equipment wear
Reduce comfort in indoor environments
Without proper isolation, these issues can lead to expensive maintenance and poor building performance.
2. Bell Mounts: The Ideal Fit for HVAC
Bell mounts offer a compact and efficient solution for isolating vibrations in HVAC systems. Their design allows them to absorb both vertical and lateral vibrations, making them ideal for:
Rooftop HVAC units
Wall-mounted fan coil units
Floor-mounted air handlers
Small duct-mounted compressors
The built-in rubber element inside the bell-shaped housing absorbs vibrations at their source, preventing them from traveling through the unit’s base to walls, ceilings, or floors.
3. Corrosion Resistance for Outdoor HVAC
Many HVAC units are installed outdoors or in damp mechanical rooms. Bell mounts are often made with galvanized or stainless steel housings, providing long-term resistance to moisture, rust, and chemical exposure — a must for HVAC environments.
4. Easy Installation in Tight Spaces
Bell mounts are easy to install with standard bolts and don’t require special tools or large clearance space. This makes them a preferred choice for HVAC contractors and engineers looking for a fast, reliable, and low-profile solution.
In conclusion, bell mounts are highly compatible with HVAC systems, offering excellent vibration control, long service life, and ease of installation. Whether for a rooftop chiller or an indoor FCU, bell mounts help HVAC equipment run smoother, quieter, and longer.
Precision equipment such as medical devices, laboratory instruments, and sensitive measuring systems require extremely stable environments to function accurately. Even minor vibrations can cause errors or damage delicate components. Controlling vibration in these applications is challenging, and choosing the right isolator is critical.
Rubber bell mounts, with their excellent vibration damping and shock absorption properties, can be a suitable solution for certain types of precision equipment, especially where moderate isolation and durability are required.
Vibration Damping Characteristics of Bell Mounts
Bell mounts use high-quality elastomer rubber that deforms elastically to absorb and dissipate vibration energy. This reduces the amplitude and frequency of vibrations transmitted to the equipment, providing a quieter and more stable operating environment.
The bell shape allows for multidirectional flexibility, isolating vibrations in vertical, lateral, and torsional directions. This is important because precision devices often experience complex vibration patterns.
Suitability for Precision Equipment
Bell mounts are ideal for precision equipment that operates within moderate vibration frequency ranges and does not require ultra-high isolation performance. Examples include:
Laboratory centrifuges
Analytical balances
Small medical imaging devices
Precision pumps and compressors
However, for extremely sensitive equipment needing sub-micron vibration isolation, specialized isolators like pneumatic or active vibration control systems may be more appropriate.
Advantages Over Other Isolation Methods
Compared to hard mounts or simple rubber pads, bell mounts offer better shock absorption and vibration damping due to their unique shape and rubber formulation. They provide:
Reliable vibration isolation in multiple directions
Resistance to environmental factors like moisture and temperature changes
Long service life with low maintenance
These features make bell mounts a practical, cost-effective choice for many precision instruments.
Installation and Maintenance Tips
Ensure mounts are sized correctly for equipment weight and vibration profile.
Install mounts symmetrically to maintain equipment balance.
Regularly inspect for rubber aging or cracks to prevent performance degradation.
Avoid excessive compression beyond the recommended load range.
Limitations
While bell mounts reduce vibration effectively, they are passive isolators and do not adapt actively to varying vibration frequencies or amplitudes. For highly sensitive precision instruments operating in ultra-low vibration environments, more advanced active isolation systems may be necessary.
Conclusion
Bell mounts can be successfully used to reduce vibration in many types of precision equipment, providing stable operation and protecting delicate components. Their multidirectional vibration isolation, durability, and ease of installation make them a popular choice for laboratory and medical devices where moderate vibration control is sufficient.
The typical load range of bell mounts varies depending on their size, rubber hardness, and intended application—but generally, they are engineered to support loads from 5 kg (11 lbs) up to 500 kg (1,100 lbs) per mount.
This broad load range makes bell mounts suitable for everything from lightweight electronic enclosures to large industrial machinery.
1. Light-Duty Applications (5–50 kg per mount)
Small bell mounts with softer rubber (Shore A 40–50) are ideal for:
Fan coil units (FCUs)
Control panels
Small pumps or motors
These mounts focus on high-frequency vibration isolation, common in smaller or fast-running equipment.
2. Medium-Duty Applications (50–200 kg per mount)
Mid-range bell mounts serve:
Air handling units (AHUs)
Wall-mounted HVAC compressors
Laboratory equipment or packaging machines
They strike a balance between flexibility and strength, offering effective shock and vibration control under moderate load conditions.
3. Heavy-Duty Applications (200–500+ kg per mount)
Heavy-duty bell mounts with reinforced housings and harder rubber (Shore A 60–70) are designed for:
Diesel generators
Industrial blowers
Marine engines or compressors
These are engineered to absorb dynamic shock loads and low-frequency vibrations, which are more intense and damaging if not properly isolated.
4. Factors That Influence Load Capacity
Rubber type & durometer: Determines elasticity and compression strength
Metal housing design: Affects structural stability and load distribution
Mount dimensions: Larger mounts tend to support more weight
Operating environment: Extreme temperatures or corrosive atmospheres may reduce long-term load capacity
5. Load Distribution Consideration
When designing with bell mounts, the total weight of the equipment should be divided by the number of mounts used. For example, if a machine weighs 800 kg and uses 4 bell mounts, each mount should be rated for at least 200 kg (with a 10–20% safety margin).
In conclusion, bell mounts offer load ranges from 5 kg to over 500 kg per unit, making them versatile enough for use in both precision and heavy-duty applications. Always consult with the manufacturer or a vibration control specialist to select the proper rating based on your system’s needs.
Bell mounts are just one of many types of vibration isolators available on the market, but they stand out for their compact design, ease of installation, and balanced vibration control. To understand where bell mounts excel, it’s useful to compare them with other common isolator types such as rubber pads, spring isolators, and air mounts.
1. Bell mounts vs. rubber isolation pads
Rubber pads are low-cost and easy to install, making them popular in residential or lightweight HVAC setups. However, they typically only provide basic vertical isolation and lack the structural support of bell mounts. In contrast, bell mounts offer controlled vibration reduction in multiple directions, especially under dynamic loads, making them more reliable in industrial and mechanical systems.
2. Bell mounts vs. spring isolators
Spring isolators are ideal for heavy machinery with low-frequency vibration, such as large AHUs or chillers. They provide excellent vertical isolation, but they are bulkier and more expensive. Bell mounts are better suited for medium-frequency applications and tight spaces where spring isolators may not fit. They also require less maintenance and offer more stable damping under fluctuating loads.
3. Bell mounts vs. air mounts
Air isolators offer high-performance active or semi-active vibration control, often used in precision equipment like lab instruments. However, they are complex, costly, and sensitive to environmental changes. Bell mounts, while passive, are robust, cost-effective, and easier to deploy across various industries, including marine, HVAC, and mobile equipment.
4. Comparison summary
Feature | Bell Mounts | Rubber Pads | Spring Isolators | Air Mounts |
---|---|---|---|---|
Vibration control | Moderate (multi-axis) | Low (mainly vertical) | High (mainly vertical) | Very High (active) |
Size & space efficiency | Very compact | Very compact | Bulky | Bulky |
Cost | Medium | Low | High | Very high |
Maintenance | Low | Very low | Medium to high | High |
Ideal applications | HVAC, marine, pumps | Appliances, light fans | Large AHUs, chillers | Lab, precision machines |
Bell mounts offer a practical middle ground, combining good vibration control, durability, and space efficiency—making them a smart choice for a wide range of general-purpose isolation needs.
Bell mounts are composed of two main parts: the internal rubber element and the external metal housing. The selection of materials for these components is crucial, as it directly affects the mount’s performance, durability, and suitability for specific environments or applications.
1. Rubber materials
The core of a bell mount is the rubber component, responsible for vibration damping and shock absorption. Common rubber materials include:
Natural rubber
Known for its excellent elasticity and energy absorption capabilities. It’s ideal for general-purpose industrial equipment where oil or chemical exposure is minimal.Neoprene rubber
Offers better resistance to oils, chemicals, ozone, and aging. Frequently used in HVAC, automotive, and marine environments where exposure to harsh conditions is expected.EPDM (Ethylene Propylene Diene Monomer)
Suitable for outdoor and high-temperature applications due to its strong resistance to weathering, UV, and heat.
Each rubber type is available in various hardness ratings (Shore A), typically ranging from 40 to 70, depending on load and vibration frequency requirements.
2. Metal housing materials
The bell-shaped outer casing is typically made of durable metals that provide structural support and protect the rubber inside. Common options include:
Galvanized steel
Cost-effective and corrosion-resistant, suitable for most indoor and covered outdoor applications.Stainless steel
Offers superior corrosion resistance in wet or marine environments. Often used in coastal installations or food-grade equipment.Aluminum
Lightweight and corrosion-resistant. Suitable for portable systems, transport equipment, or applications with weight limitations.
Some manufacturers also apply powder coating or paint finishes to improve corrosion protection and aesthetics, especially in exposed environments.
3. Other components
Depending on the mount design and application, bell mounts may include:
Internal washers or bushings for load distribution
Threaded inserts or bolts for direct mounting
Labeling or color-coded rubber for identification and load rating
These additional components are typically made of zinc-plated steel, stainless steel, or engineered plastics, depending on requirements.
In summary, bell mounts are built from a combination of high-performance rubber and protective metal housing materials. The choice of rubber and metal depends on the application’s specific needs, including load, vibration frequency, temperature, and environmental exposure.
One of the key advantages of bell mounts is their low-maintenance design. Unlike complex isolation systems such as air springs or hydraulic mounts, bell mounts are passive components with no moving parts or pressure systems that require regular servicing. However, while they are largely maintenance-free, there are a few essential checks that help ensure long-term performance.
1. Routine visual inspection
It’s recommended to perform a simple visual check of the bell mounts during scheduled equipment maintenance—typically once or twice per year. Look for:
Cracks or deformation in the rubber
Signs of aging, such as hardening or discoloration
Corrosion or damage on the metal housing
Loose or missing bolts
Early detection of wear can prevent larger mechanical issues and ensure continuous vibration control.
2. Rubber aging over time
Although high-quality rubber compounds like neoprene and EPDM are engineered to resist environmental degradation, all rubber materials gradually age due to:
Heat exposure
Ozone and UV light
Oil or chemical contact
Over several years of operation, the rubber may lose elasticity, reducing its effectiveness. In such cases, replacement is usually recommended every 5–8 years, depending on the operating environment.
3. Environmental considerations
Bell mounts used in outdoor, marine, or chemical-heavy environments should be checked more frequently. Stainless steel housings and chemically resistant rubber can extend lifespan, but regular inspection helps mitigate unforeseen failures caused by harsh conditions.
4. Tightness check
Vibration over time may cause mounting bolts to loosen. As part of routine maintenance, ensure that the bell mount bolts remain properly torqued to prevent shifting or misalignment.
5. No lubrication or calibration needed
Unlike spring isolators or dynamic vibration control systems, bell mounts do not require lubrication, recalibration, or adjustment, making them an attractive choice for applications where maintenance access is difficult or costly.
In conclusion, while bell mounts are essentially maintenance-free, periodic visual inspections and environmental awareness can greatly extend their service life and reliability. Their robust construction makes them ideal for long-term use in both industrial and HVAC systems.
Yes, bell mounts can be effectively used in marine and outdoor environments, provided they are made with the right combination of materials and protective finishes. Their ability to isolate vibration and absorb shock makes them especially valuable in challenging conditions like those found on ships, docks, HVAC rooftops, and outdoor generators.
1. Material selection is critical
In outdoor or marine use, bell mounts are exposed to moisture, salt air, UV radiation, and temperature changes. To withstand these conditions, manufacturers typically use:
Stainless steel housings (304 or 316 grade): Highly resistant to rust and corrosion, even in salty or humid environments.
Neoprene or EPDM rubber: These rubber types offer excellent resistance to ozone, salt spray, water, and temperature extremes.
When both the metal and rubber components are marine-grade, the bell mount can function reliably for years in exposed conditions.
2. Common marine applications
Bell mounts are often found in:
Marine engine mounts
Onboard HVAC units or compressors
Pumps and control panels in ships or offshore platforms
Dockside generators or utility units
Their compact shape and multi-axis vibration isolation are well-suited for use on vessels where space is limited and vibration sources are intense.
3. Outdoor equipment uses
Bell mounts also perform well in:
Rooftop air handling units (AHUs)
Wall-mounted condensers or compressors
Outdoor backup generator sets
Solar inverter enclosures
They help reduce noise transmission and vibration transfer to walls or rooftop structures, improving comfort and protecting sensitive equipment.
4. Protective coatings and installation practices
For added durability, some bell mounts feature:
Powder-coated housings for extra corrosion resistance
Drain holes or slotted bases to prevent water accumulation
UV-stabilized rubber compounds to reduce cracking under sun exposure
Proper mounting, sealing, and occasional inspection will further improve long-term performance in outdoor environments.
In summary, bell mounts are fully capable of withstanding marine and outdoor conditions—as long as the correct materials and finishes are selected. Their rugged, sealed construction and vibration-damping efficiency make them an ideal choice for harsh environmental applications.
Proper installation of bell mounts is essential to ensure optimal vibration isolation and long-term durability. Although bell mounts are designed for ease of installation, following best practices helps maximize their effectiveness and prevent premature failure.
1. Choose the correct mount type
Before installation, verify that the selected bell mount:
Matches the weight and center of gravity of the equipment
Is rated for the expected vibration frequency
Has the appropriate rubber hardness (Shore A) for the load
Also, check whether the mount is designed for vertical, horizontal, or multi-directional isolation.
2. Ensure even load distribution
Distribute the weight of the equipment equally across all bell mounts. For example, if the machine weighs 400 kg and uses four mounts, each mount should be rated for at least 100 kg, with an additional 10–20% safety margin.
Avoid overloading one side, as this can reduce isolation performance and lead to mount damage.
3. Mounting surface preparation
Ensure that both the equipment base and the floor or support structure are:
Flat, clean, and level
Free from oil, rust, or debris
Structurally sound to support dynamic loads
This helps ensure full contact and prevents slippage or misalignment.
4. Bolt tightening and alignment
Insert the bell mounts into pre-drilled holes using bolts or threaded studs
Tighten bolts evenly and gradually, using a crisscross pattern if necessary
Avoid over-tightening, which can compress the rubber excessively and reduce damping efficiency
Use lock washers or thread-locking compounds to prevent bolt loosening due to vibration
Some bell mounts include a top cover or washer that must sit snugly against the base plate for optimal performance.
5. Check for thermal and vibration expansion space
Allow a small clearance around the mounted equipment to account for:
Rubber compression and rebound movement
Thermal expansion or contraction of metal parts
This prevents parts from rubbing against surrounding structures, which can create noise or wear.
6. Post-installation inspection
After installation:
Verify that the equipment is level
Confirm that all mounts are carrying weight evenly
Check for any unusual noises or vibrations during initial operation
Periodic rechecks after the first few days of use help catch any early issues such as bolt loosening.
In conclusion, installing bell mounts correctly involves selecting the right type, distributing the load evenly, preparing the surfaces, and tightening components with care. These simple steps ensure reliable vibration isolation and extend the lifespan of both the mounts and the supported equipment.