Center Bonded Mounts
High-Performance Center Bonded Mounts for Vibration and Shock Isolation
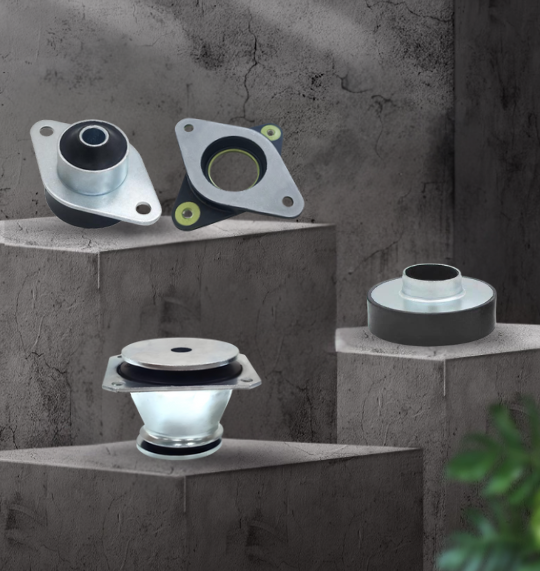
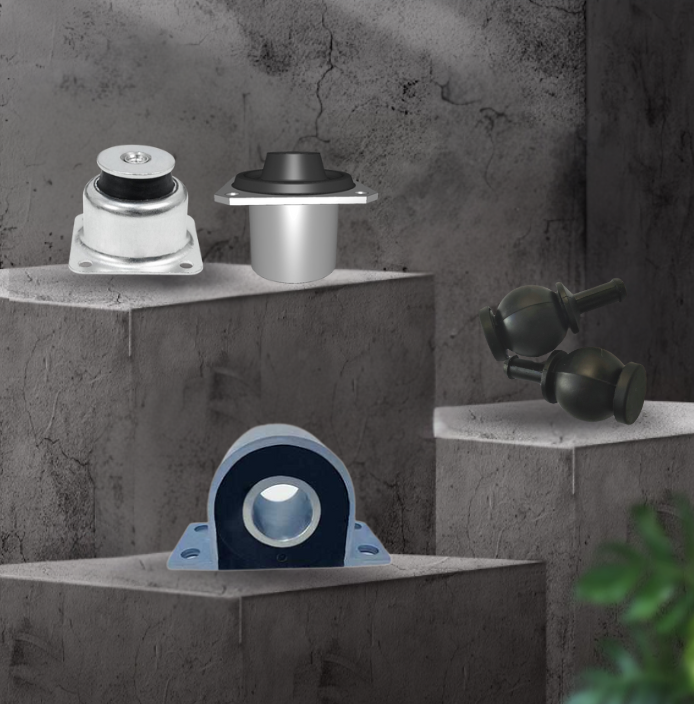
Our products
Center Bonded Mounts
- CN Series Cone Mounts
- Hydraulic Cone Mounts
- GY Series Hydraulic Mount
- Semi-Circular Support Kit
- CGM Series Ring Buffer
- CNU Anti Vibration Mounts
- ST Stepper Motor Damper
- Silicone Viscous Damper
Product Showcase
Center Bonded Mounts for Industrial Machiner
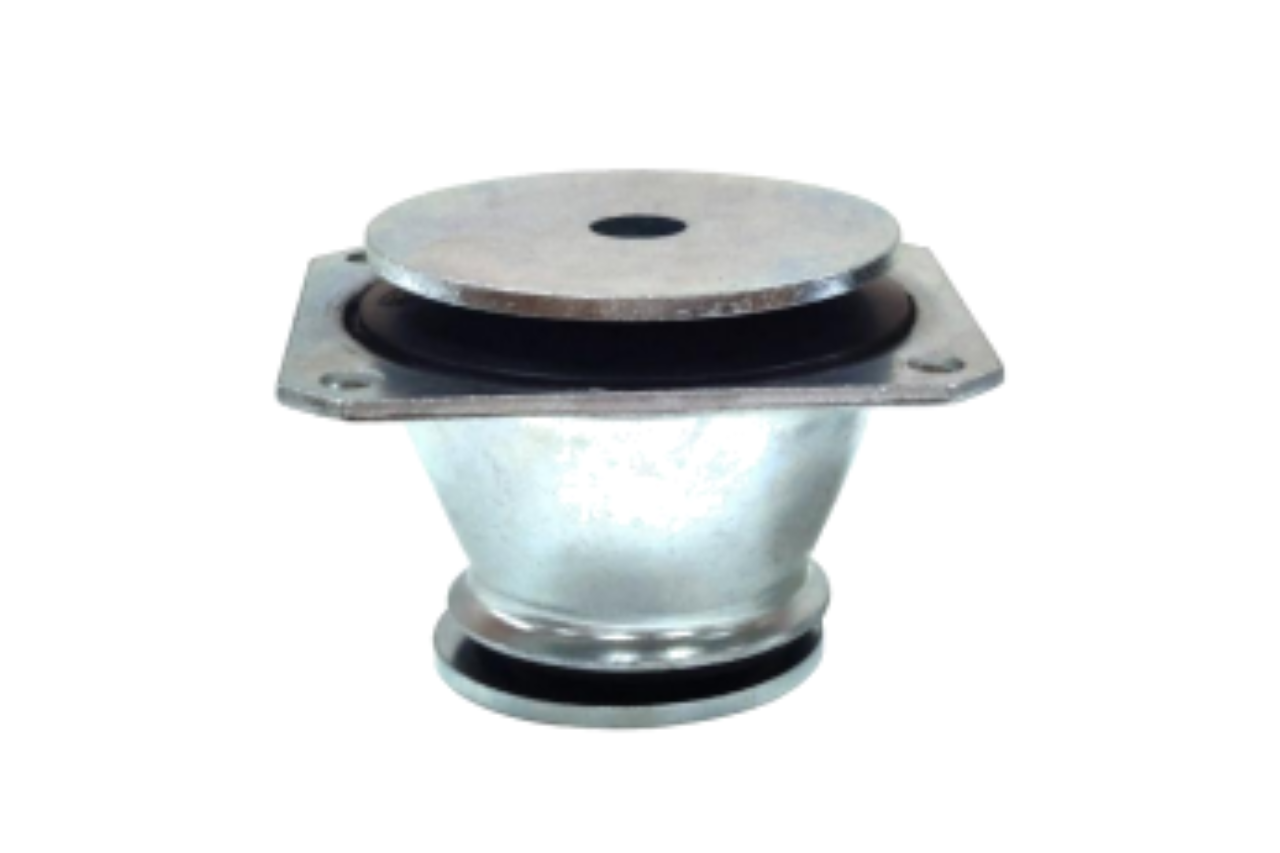
Cone Mounts
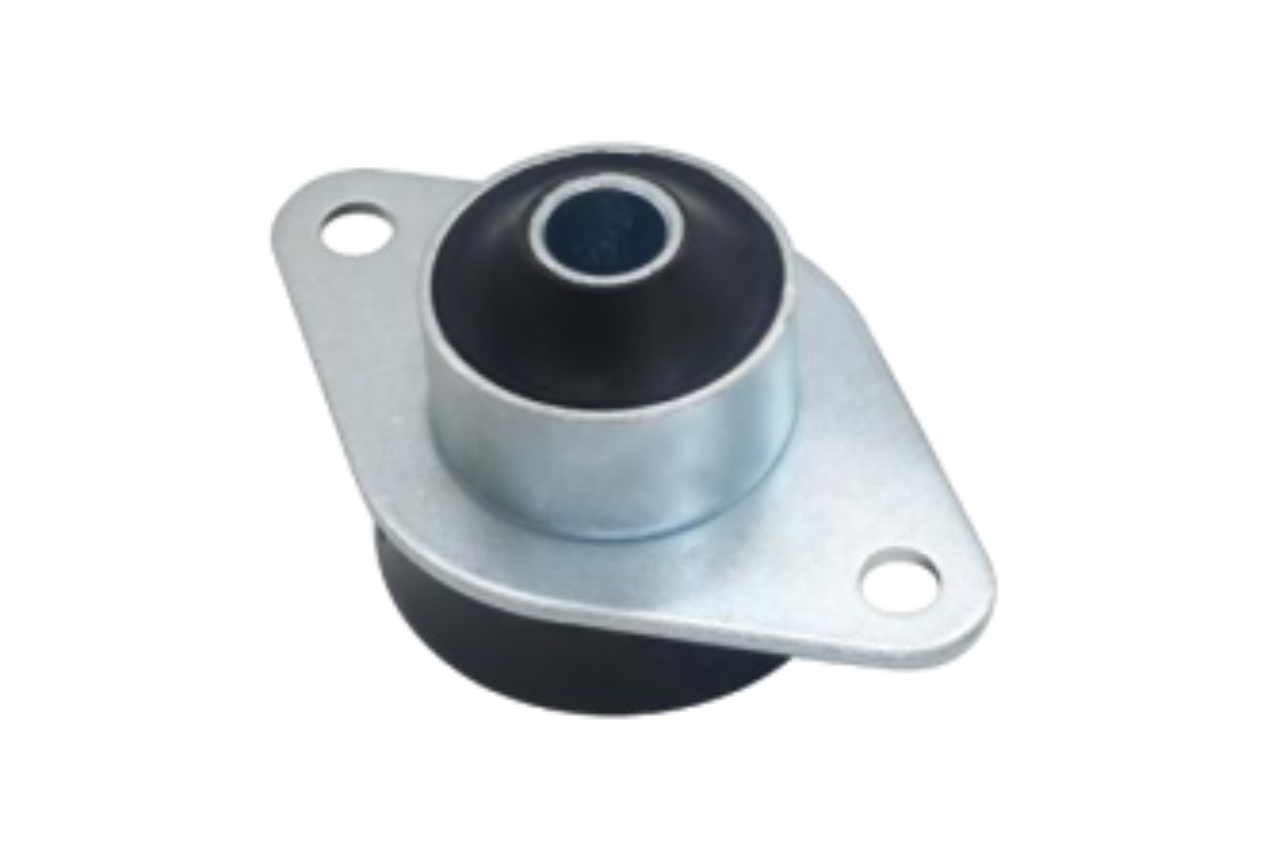
Cone Mounts
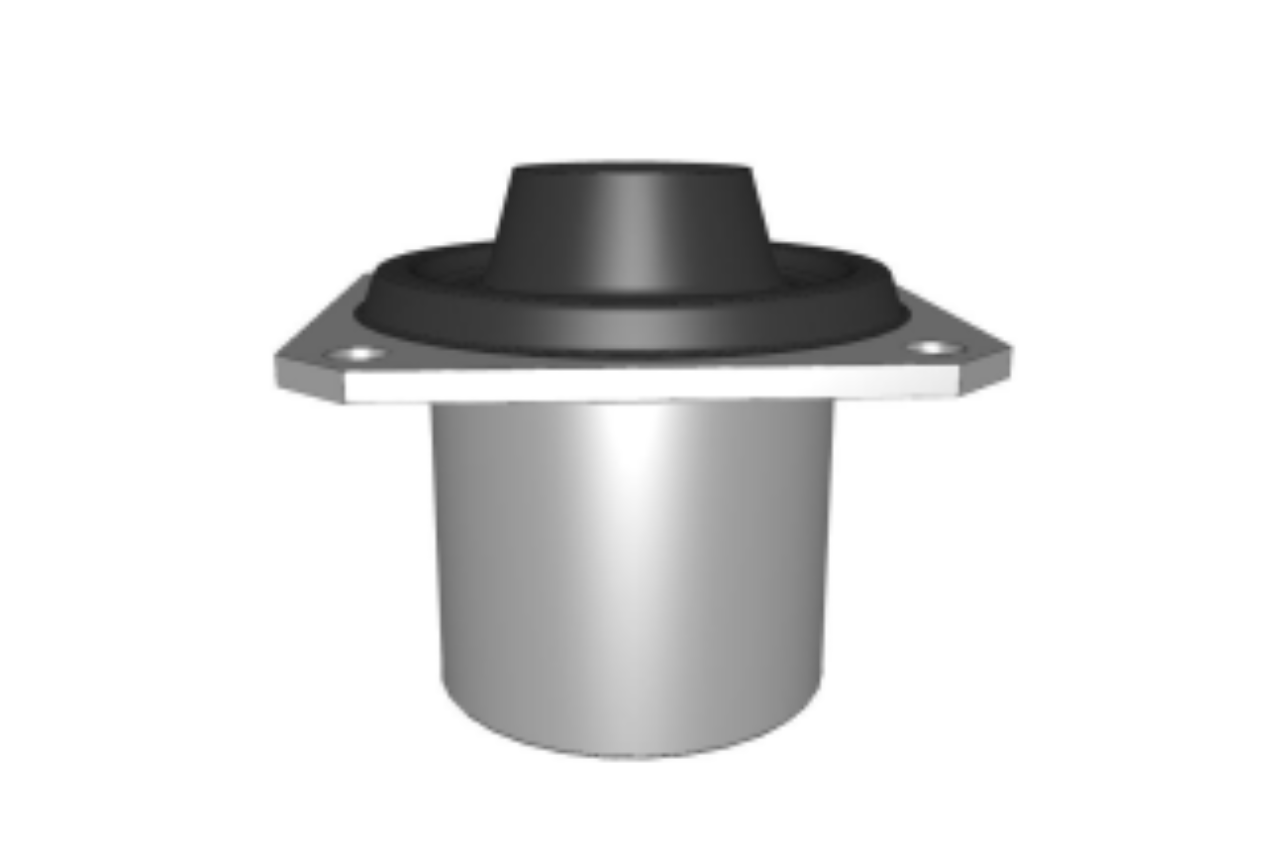
Hydraulic Mount
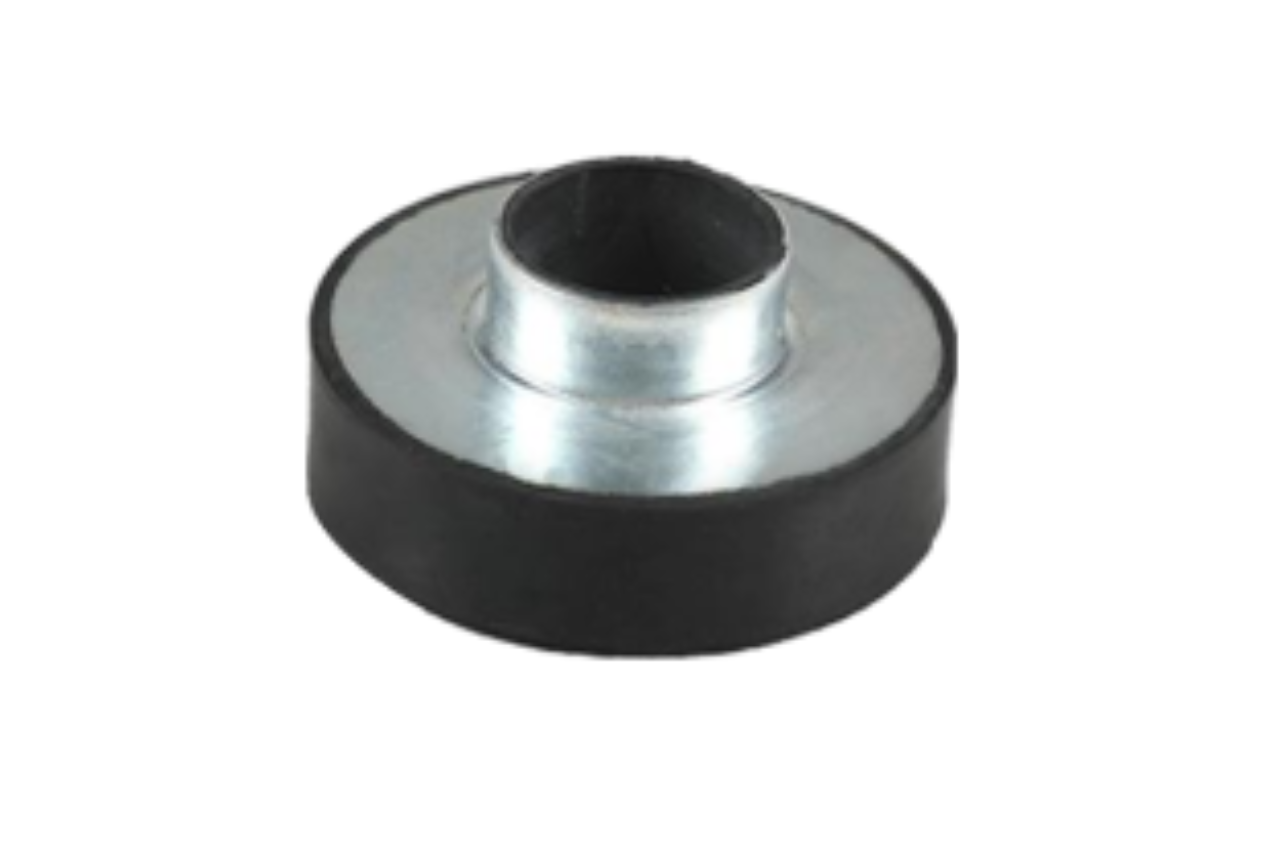
Vibration Buffer
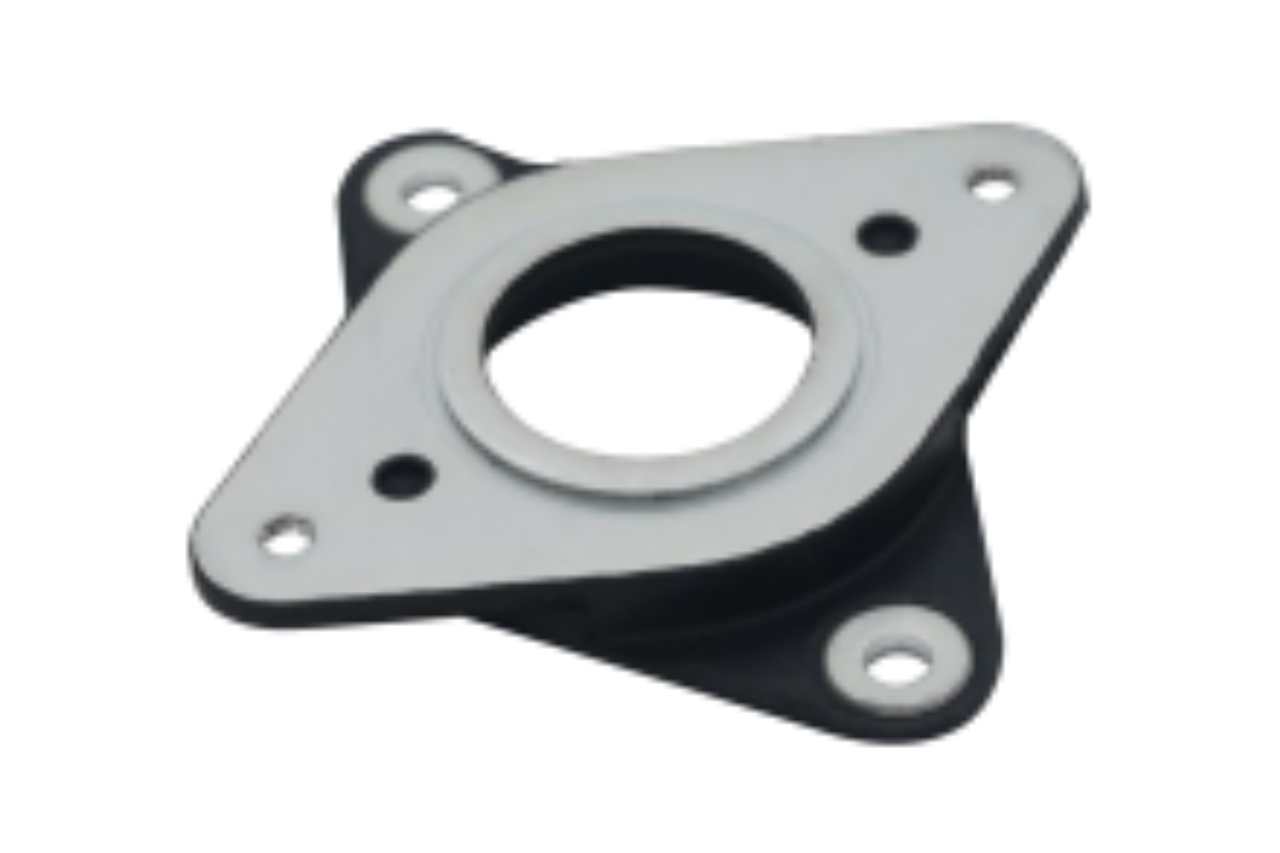
Motor Damper
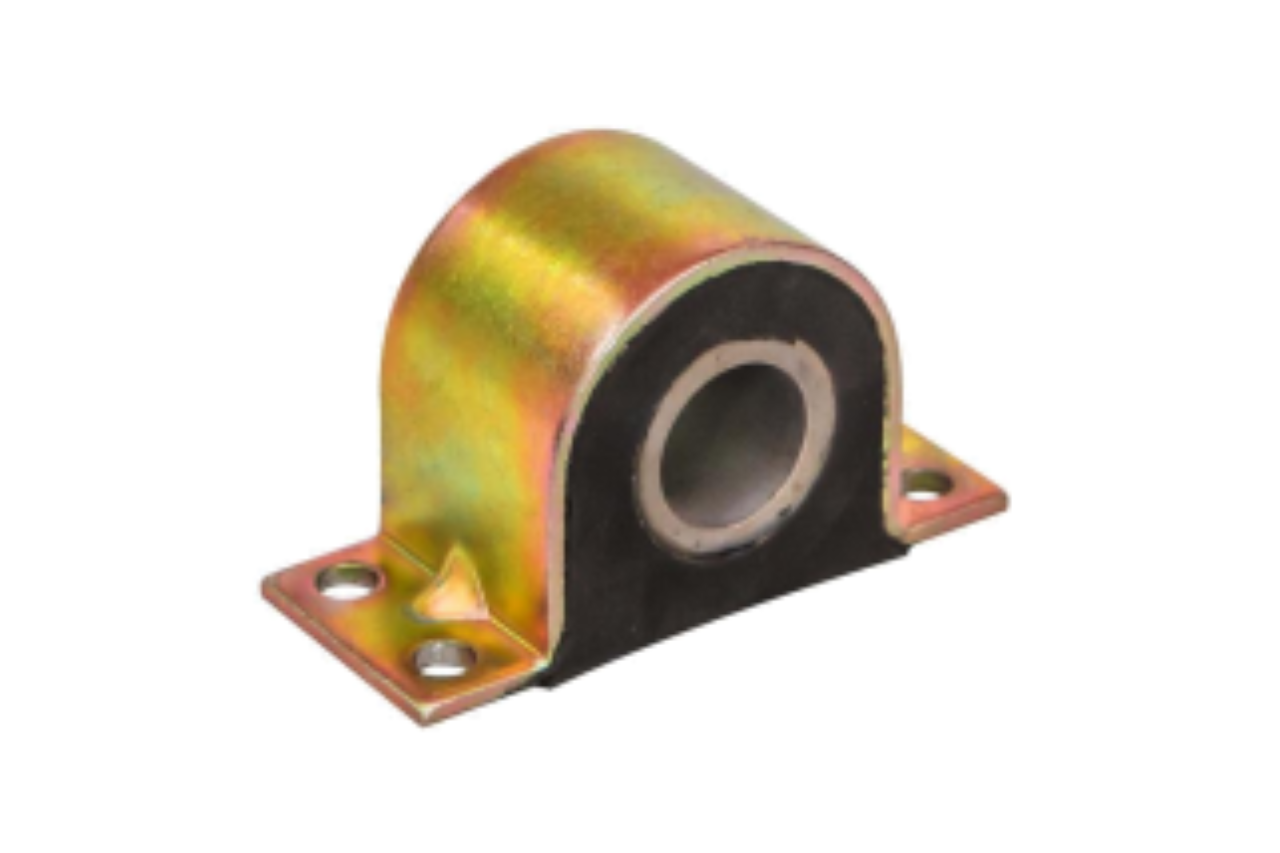
Vibration Mounts
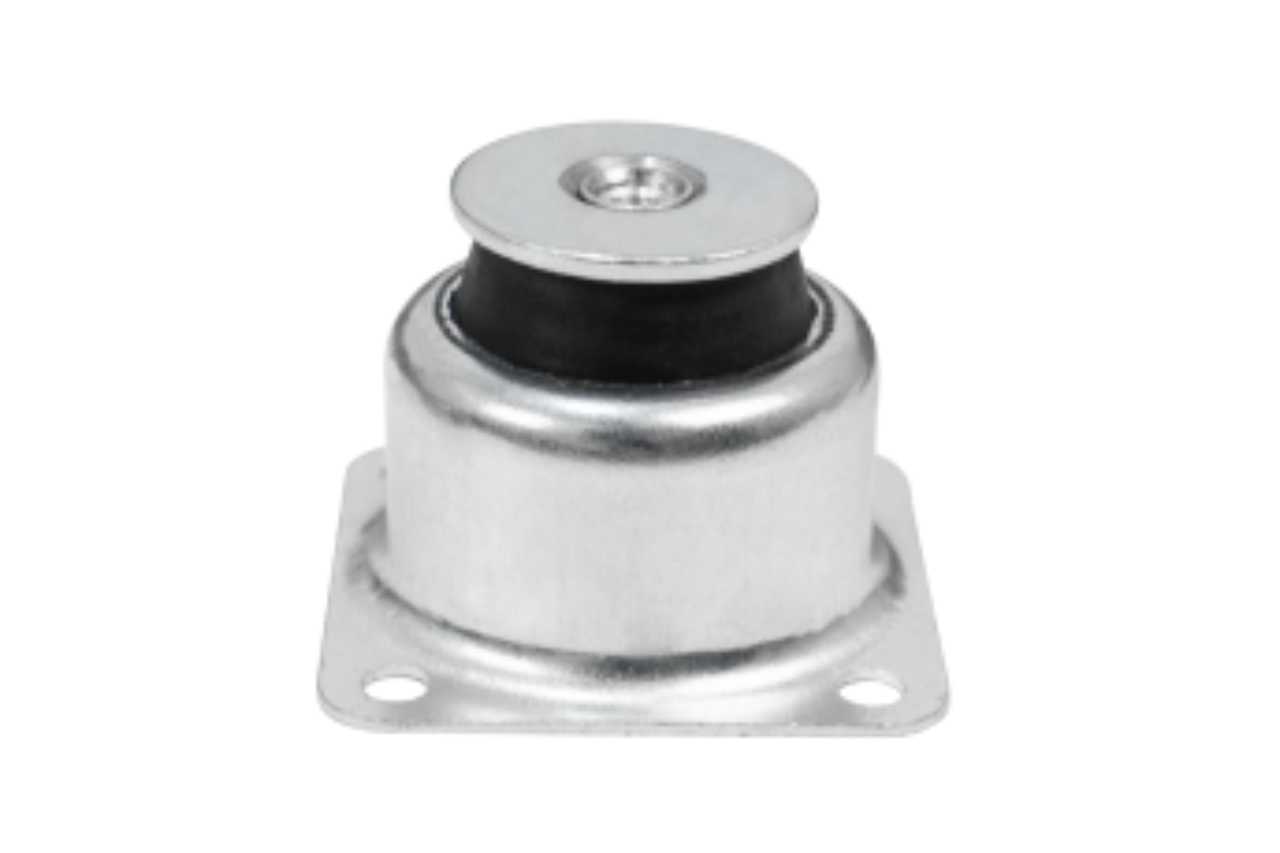
Vibration Dampe
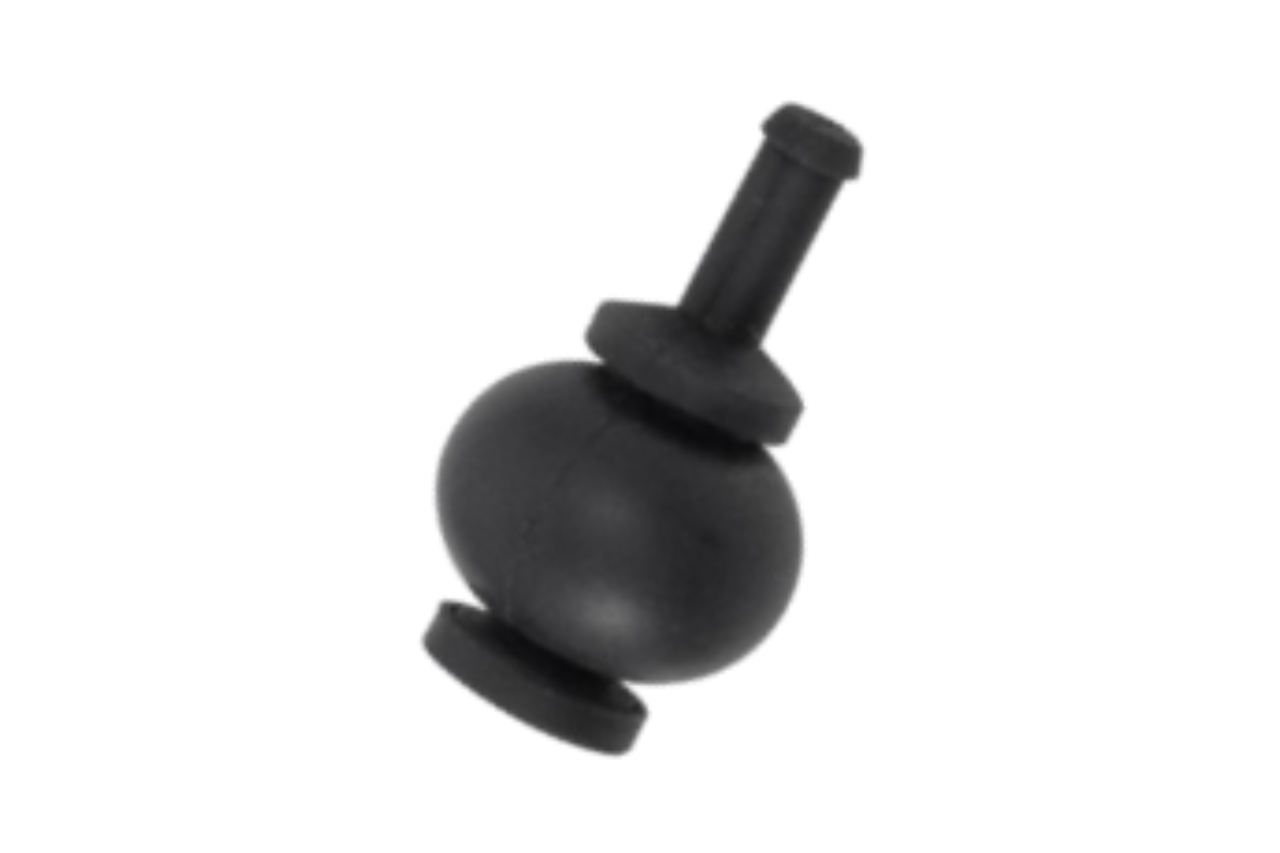
Vibration Dampe
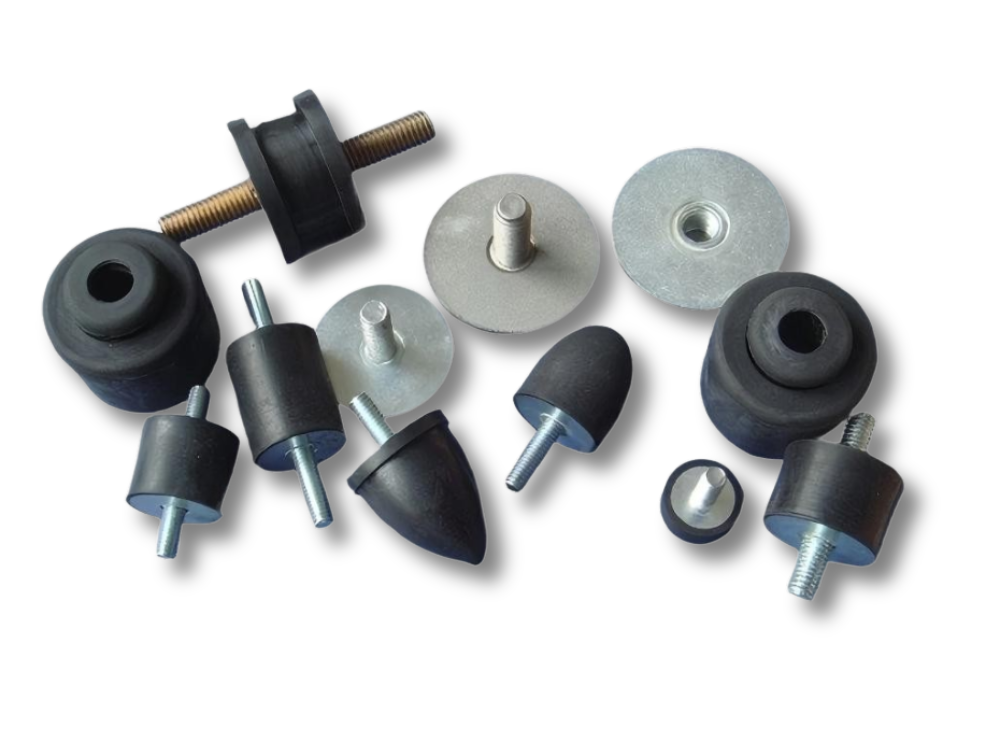
Vibration Dampe
Why Choose Us
Trusted Rubber Vibration Isolator Manufacturer with 30 Years of Expertise
Factory-direct solutions with natural rubber, customizable options, reliable quality, and trusted performance.
We own and operate our factory, ensuring strict quality control, stable lead times, and support for small-batch customization
With over three decades in vibration isolation, we offer trusted solutions backed by rich technical knowledge and real-world application.
Our isolators use pure natural rubber for excellent elasticity, durability, and superior shock absorption compared to synthetic materials.
Our ISO-compliant production lines and testing systems ensure consistent quality and reliable performance across all batches.
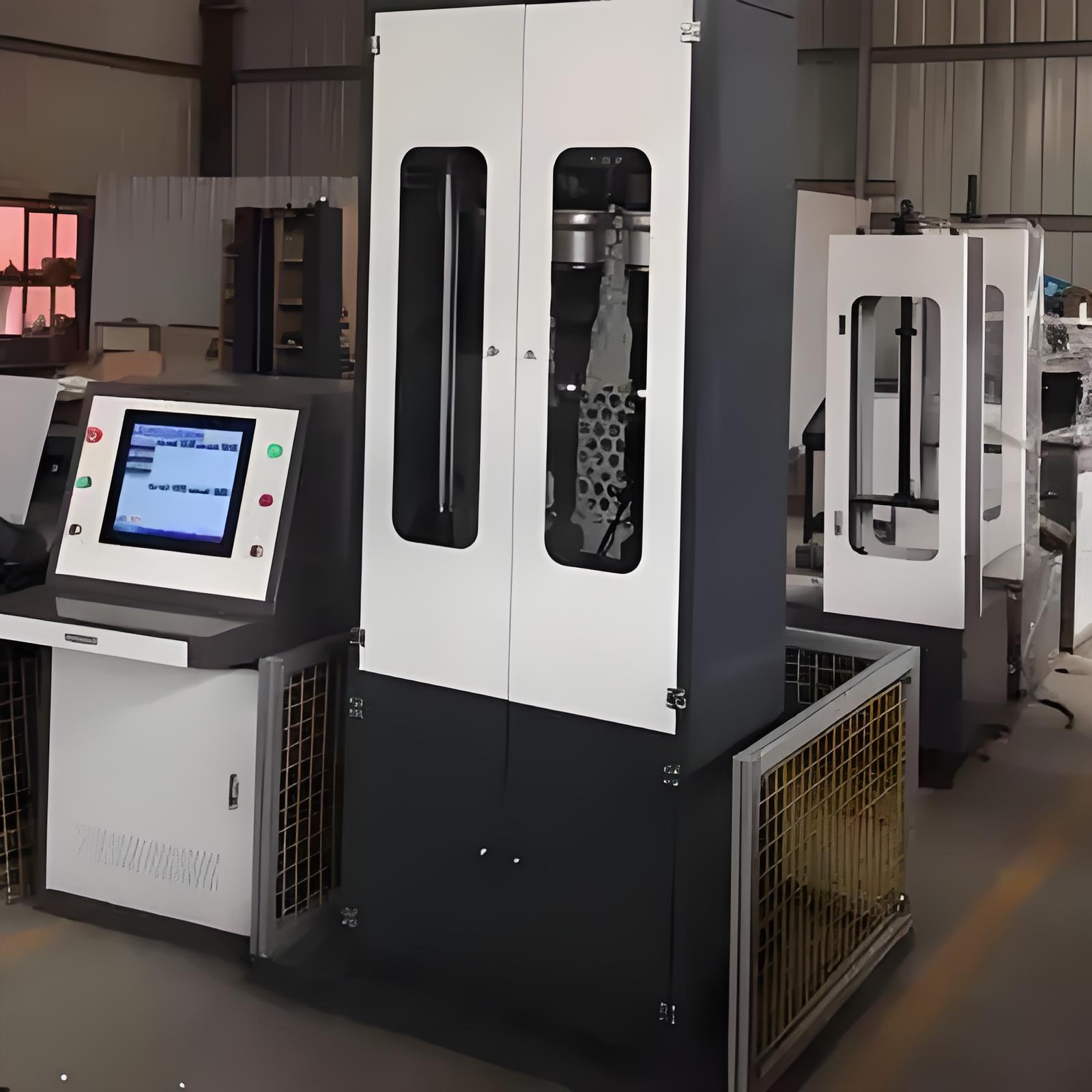
+86 13032112360
Common Questions
Most Popular Questions
A center bonded mount is a widely used elastic support element for vibration isolation in mechanical equipment. It consists of a rubber layer firmly bonded between two metal plates through a vulcanization process, forming an integrated structure. This "center bonding" process ensures a strong adhesion between the rubber and metal parts, resulting in excellent load-bearing and vibration isolation performance.
Structure Components:
Metal Base: Typically made of steel or aluminum plates, providing mechanical support and mounting interface.
Rubber Layer: Placed between the two metal plates, acting as an elastic material that absorbs and cushions vibration energy. Common rubber types include natural rubber, neoprene, nitrile rubber, or silicone rubber, all offering good elasticity and damping characteristics.
Bonding Layer: Through a high-temperature vulcanization process, the rubber chemically and mechanically bonds to the metal surface, ensuring a firm and durable connection without delamination.
Working Principle:
When the equipment operates, mechanical vibrations and shock forces are transmitted to the mount. The rubber deforms elastically and its internal friction provides damping, absorbing vibration energy and partially converting it into heat. This significantly reduces the transmission of vibrations to the equipment foundation or support structure. It not only lowers operational noise but also decreases mechanical fatigue and damage, enhancing equipment stability and service life.
Main Functions:
Vibration Isolation: Effectively isolates mechanical vibrations to prevent structural damage and noise pollution caused by vibration transmission.
Shock Absorption: Cushions shock forces during equipment startup, shutdown, or sudden loads, protecting mechanical components.
Noise Reduction: Reduces noise generated by equipment vibrations, improving workplace comfort.
Load Support: Provides mechanical support to ensure stable equipment installation and withstands static and dynamic loads.
Application Advantages:
The firm bonding of rubber and metal provides higher load capacity and durability.
Compact structure saves installation space.
Suitable for multi-directional vibrations, especially in complex vibration environments.
Rubber hardness and material can be customized to meet various requirements such as temperature resistance, oil resistance, and corrosion resistance.
Easy installation and maintenance, suitable for large-scale industrial applications.
Typical Applications:
Engine and engine mounts, fans, pumps, compressors, air conditioning equipment, agricultural machinery, industrial automation equipment, and other scenarios requiring effective vibration isolation and stable support.
Center bonded mounts boast multiple significant advantages due to their unique structural design and manufacturing process, making them widely used in vibration isolation for mechanical equipment.
1. Robust and Integrated Structure
Through a high-temperature vulcanization process, the rubber is firmly bonded between the upper and lower metal plates, forming a seamless integrated structure. This design effectively prevents delamination or slipping between the rubber and metal, enhancing overall load capacity and stability.
2. Excellent Vibration Isolation Performance
The elasticity and damping properties of the rubber enable the center bonded mount to absorb and cushion multi-directional vibrations and shocks generated during equipment operation, effectively reducing the vibration transmitted to foundations or supports and protecting both the equipment and its installation environment.
3. High Durability and Long Service Life
Due to the firm bonding, the rubber layer will not separate from the metal plates under load and vibration, reducing the risk of fatigue failure. Additionally, rubber materials can be selected with special properties such as oil resistance, high-temperature resistance, and corrosion resistance, allowing them to adapt to harsh working environments and extend service life.
4. Easy Installation and Space Saving
Center bonded mounts have a compact, typically one-piece design that allows for quick installation and maintenance. Compared to traditional mechanical connection methods, they save installation space and labor costs, improving overall equipment assembly efficiency.
5. Strong Load Capacity and Adaptability
These mounts can withstand considerable static and dynamic loads, making them suitable for complex working conditions such as high-speed rotation, large vibration amplitudes, and heavy shocks, ensuring stable equipment operation.
6. Multi-Directional Vibration Isolation
Unlike isolators that only address vibrations in a single direction, center bonded mounts can isolate vibrations in vertical, horizontal, and shear directions simultaneously, enhancing the overall effectiveness of the vibration isolation system.
7. Customizable Materials
Depending on specific application requirements, different rubber hardness levels (Shore A ratings) and types of rubber (natural rubber, neoprene, nitrile rubber, etc.) can be chosen to meet diverse needs such as temperature resistance, oil resistance, aging resistance, and corrosion resistance.
These advantages make center bonded mounts an ideal choice for vibration isolation systems in engines, pumps, fans, compressors, air conditioning equipment, and other industrial machinery.
Center bonded mounts are versatile vibration isolation components widely used across various industries due to their excellent performance, durability, and adaptability. Their unique design makes them ideal for applications requiring reliable vibration damping and stable equipment support.
1. Automotive Industry
Center bonded mounts are commonly used in engine mounts, transmission mounts, and exhaust system supports. They help reduce engine vibrations and noise transmitted to the vehicle chassis, improving ride comfort and protecting sensitive components.
2. Industrial Machinery
In industrial settings, these mounts support pumps, compressors, fans, blowers, and generators. By isolating vibrations, they prevent structural damage, reduce noise pollution, and enhance the longevity of heavy machinery.
3. HVAC Systems
Heating, ventilation, and air conditioning equipment often uses center bonded mounts to dampen vibrations from motors and fans. This improves system reliability, reduces operational noise, and extends equipment service life.
4. Agricultural Equipment
Agricultural machinery such as tractors, harvesters, and irrigation pumps benefit from these mounts by reducing shock loads and vibration transmission, thereby enhancing machine durability and operator comfort.
5. Marine and Offshore Applications
Center bonded mounts are suitable for marine engines and auxiliary equipment where vibration control is critical for safety and equipment performance in harsh environments.
6. Renewable Energy Equipment
Wind turbines and other renewable energy machines employ these mounts to isolate vibrations from rotating components, minimizing wear and tear and improving system stability.
7. Electronics and Precision Equipment
Sensitive equipment requiring minimal vibration interference, such as medical devices, laboratory instruments, and precision manufacturing tools, use center bonded mounts to ensure operational accuracy and longevity.
Their adaptability to various load conditions and environments makes center bonded mounts indispensable across these diverse application areas, contributing to improved equipment performance, safety, and longevity.
Center bonded mounts are commonly integrated into equipment that demands efficient vibration control, structural stability, and long-term durability. Their compact, robust design makes them ideal for both mobile and stationary applications across a wide range of industries.
1. Engines and Generators
Gasoline and diesel engines, as well as industrial generators, rely on center bonded mounts to isolate engine vibration, reduce noise, and prevent fatigue in support structures.
2. Pumps and Compressors
Centrifugal pumps, vacuum pumps, and air compressors generate high-frequency vibrations that center bonded mounts effectively dampen, protecting connected piping and structural frames.
3. HVAC Units
Air handling units (AHUs), fan coil units (FCUs), and rooftop HVAC systems use these mounts to reduce vibration transmission from rotating fans or motors, improving comfort and reducing wear.
4. Industrial Fans and Blowers
Center bonded mounts are suitable for supporting high-speed industrial fans and blowers, ensuring balanced operation and preventing vibration-related damage.
5. Construction and Earthmoving Equipment
In vehicles such as bulldozers, excavators, and backhoes, these mounts help dampen engine and chassis vibration, enhancing operator comfort and equipment durability.
6. Marine Equipment
On boats and ships, center bonded mounts are used with propulsion systems and auxiliary machines to minimize the impact of engine vibrations in confined spaces.
7. Laboratory and Medical Devices
Sensitive machines like microscopes, imaging devices, and analyzers employ these mounts to maintain operational accuracy by isolating ambient or internal vibrations.
Center bonded mounts play a critical role in vibration isolation systems by effectively reducing the transmission of vibrations and shocks between machinery and its supporting structures. Their unique construction—rubber bonded between two metal plates—allows for durable and multi-directional damping, which is essential for protecting equipment performance and structural integrity.
1. Multi-Directional Vibration Control
Center bonded mounts isolate vibrations in vertical, horizontal, and shear directions. This 3D isolation capability is especially important for dynamic equipment such as engines, pumps, and fans that operate with complex motion profiles.
2. Prevents Structural Fatigue and Damage
By absorbing operational vibrations and shocks, these mounts reduce stress transmission to the base frame or housing, minimizing fatigue cracking, loosening of bolts, and other structural issues.
3. Improves Equipment Longevity and Reliability
Effective vibration isolation protects sensitive components, bearings, and electrical systems from long-term damage, significantly extending the service life of the entire machine.
4. Enhances Operator Comfort and Safety
In mobile or human-operated machinery, reducing transmitted vibration helps lower noise levels and physical strain, improving working conditions and preventing fatigue-related risks.
5. Ensures Consistent System Performance
Vibration interference can disrupt precision operations or cause system instability. Center bonded mounts stabilize system performance, particularly in automation, medical, and measurement systems.
Center bonded mounts offer a range of mechanical and economic benefits that make them an excellent choice for vibration isolation across industries. Their design ensures efficient vibration control, ease of installation, and long-term performance reliability.
1. Compact and Durable Structure
Their simple yet robust structure—rubber bonded between two metal plates—ensures long service life even in harsh environments, with minimal maintenance required.
2. Excellent Vibration Damping
Center bonded mounts provide effective vibration and shock absorption in all directions, protecting machinery from wear, misalignment, and operational instability.
3. Easy to Install and Replace
These mounts are designed for easy mounting and replacement, reducing downtime and maintenance labor in industrial settings.
4. Cost-Effective Solution
Compared to more complex isolation systems, center bonded mounts are relatively inexpensive, offering reliable vibration control at a low cost.
5. Versatile Application Range
They are available in different sizes, hardness levels, and configurations, making them adaptable to a wide range of machines and environmental conditions.
Center bonded mounts are designed to offer quick installation and minimal maintenance, making them a reliable solution for many vibration control applications. Proper handling during installation and periodic inspection can ensure optimal performance and extended service life.
1. Installation Guidelines
Center bonded mounts are typically installed by bolting the top and bottom metal plates to the machine and base respectively. It is important to align the mount correctly and apply proper torque to avoid overstressing the rubber element.
2. Pre-Installation Checks
Before installation, verify that the load capacity of the mount matches the equipment weight and that the mounting surfaces are clean, flat, and free of oil or debris.
3. Maintenance Requirements
These mounts require very little maintenance. Periodic visual inspections (e.g., every 6–12 months) should be performed to check for signs of rubber cracking, deformation, or corrosion on the metal parts.
4. Replacement Recommendations
If the rubber shows signs of hardening, cracking, or detachment from the metal plates, the mount should be replaced immediately to avoid vibration transfer and equipment damage.
5. Environmental Considerations
Avoid exposing the mounts to oils, solvents, or UV rays that can degrade rubber over time. For harsh conditions, choose mounts with protective coatings or oil-resistant rubber compounds.
Choosing the right center bonded mount is essential for achieving effective vibration isolation and extending equipment life. Several key factors must be evaluated to ensure optimal performance and compatibility with the application.
1. Load Capacity
The mount must be able to support the static and dynamic loads of the equipment. Underloading or overloading can reduce isolation efficiency or damage the mount.
2. Frequency Range
Different mounts perform better within certain frequency ranges. Select a mount that effectively isolates the dominant vibration frequencies of the system.
3. Operating Environment
Consider exposure to oil, chemicals, moisture, and temperature extremes. Choose materials like neoprene or silicone rubber for specific resistance needs.
4. Direction of Vibration
Some applications require isolation in multiple directions. Center bonded mounts can offer multidirectional damping, but the design must align with expected motion.
5. Size and Installation Constraints
Ensure the mount’s size and bolt pattern match the available space and existing mounting configurations on the machine or equipment.
6. Durability and Life Expectancy
For long-term use, select mounts from reliable manufacturers using high-quality rubber compounds and corrosion-resistant metal parts.
Yes, center bonded mounts are well-suited for dynamic applications that involve continuous movement, vibration, or shock. Their bonded construction and symmetrical design provide balanced damping performance, making them a reliable choice for rotating and reciprocating machinery.
1. High Resilience to Dynamic Loads
Center bonded mounts are designed to handle repetitive and fluctuating loads without fatigue, making them ideal for engines, compressors, and pumps operating at varying speeds.
2. Torsional and Axial Vibration Control
Their structure allows for excellent torsional and axial vibration damping, which is especially beneficial in dynamic systems with multi-axis movement or misalignment.
3. Enhanced Service Life
Thanks to their compact design and internal bonding between rubber and metal, these mounts can withstand long-term dynamic stress with minimal degradation.
4. Noise and Shock Absorption
Besides vibration, they are also effective in reducing shock impact and mechanical noise, which is common in high-speed and heavy-duty applications.
Yes, center bonded mounts can be extensively customized to meet the specific and often demanding requirements of special applications. Customization ensures that the mounts provide optimal vibration isolation, durability, and fitment for unique operational conditions and equipment designs.
1. Custom Load and Deflection Characteristics
The mechanical properties of the mounts, such as stiffness and damping, can be tailored precisely. This involves adjusting rubber hardness, thickness, and bonding methods to support the exact static and dynamic loads the equipment experiences. For sensitive instruments requiring minimal vibration, softer compounds and higher deflection mounts can be designed, whereas heavy industrial machines might need mounts with higher load capacities and stiffer rubber formulations.
2. Material Selection Based on Environment
Depending on the environment where the mounts will be used, the rubber compound can be selected or formulated accordingly. For example, neoprene offers good oil and chemical resistance, silicone excels in high and low temperature extremes, and natural rubber provides excellent mechanical properties for general use. The metal components can also be treated with corrosion-resistant coatings or made from stainless steel to enhance longevity in harsh environments such as marine or chemical plants.
3. Special Mounting and Interface Options
Customizing mounting interfaces is critical for integration into non-standard or proprietary equipment. Options include altering bolt patterns, stud sizes, flange designs, or even adding features like threaded inserts or captive nuts. These modifications facilitate easier installation and ensure a secure fit that maintains isolation performance over time.
4. Branding and Compliance
Manufacturers often offer customization options to align with customer branding needs, including color coding, laser engraving, or molded logos. Additionally, customized products can be designed to meet specific regulatory standards such as RoHS (Restriction of Hazardous Substances), REACH (Registration, Evaluation, Authorization and Restriction of Chemicals), or other regional certifications, making them suitable for export and compliance with international market requirements.
5. Engineering Support and Prototyping
Many suppliers provide engineering consultations, finite element analysis (FEA), and prototype development to optimize mount design before full production. This collaboration ensures the customized mounts perform as intended under real-world conditions and helps reduce costly iterations.
Proper installation of center bonded mounts is crucial to ensure optimal vibration isolation performance and longevity. Incorrect installation can lead to reduced effectiveness, premature wear, or even failure of the mounts.
1. Preparation Before Installation
Before installation, inspect the mounts for any visible damage or defects. Verify that the mounts meet the specifications for load capacity, size, and material suitable for your equipment and application. Clean the mounting surfaces to remove dirt, oil, or rust to ensure good bonding and stability.
2. Correct Orientation and Alignment
Center bonded mounts must be installed in the correct orientation, typically with the bonded rubber section centered between the metal parts. Proper alignment ensures even load distribution and prevents uneven wear or deformation. Use alignment tools if necessary to achieve precise positioning.
3. Secure Fastening Without Over-Tightening
Tighten bolts or studs to the manufacturer’s recommended torque specifications. Over-tightening can compress or damage the rubber layer, reducing the mount’s isolation capabilities. Conversely, insufficient tightening can cause movement and noise. Use a calibrated torque wrench for accuracy.
4. Avoid Lateral Loads and Misalignment
Center bonded mounts are designed primarily for axial and radial loads. Excessive lateral forces or misalignment can cause premature failure. Ensure the equipment is properly supported and aligned to minimize side loads.
5. Periodic Inspection and Maintenance
Although center bonded mounts are generally maintenance-free, periodic visual inspections are recommended to check for cracks, hardening, or other signs of wear. Replace mounts showing signs of degradation to maintain effective vibration isolation.
6. Follow Manufacturer’s Instructions
Always refer to the specific installation guidelines provided by the mount manufacturer, as some models may have unique requirements or recommendations.
Center bonded mounts are primarily composed of two main materials: rubber and metal. The choice and quality of these materials directly influence the mount’s performance, durability, and suitability for various environments.
1. Rubber Compounds
The rubber component is the core element responsible for vibration damping. Common rubber materials used include:
Natural Rubber (NR): Offers excellent mechanical properties, high tensile strength, and good resilience. Suitable for general industrial applications with moderate temperature and chemical exposure.
Neoprene Rubber (CR): Known for its good oil, ozone, and weather resistance, making it ideal for automotive and outdoor applications.
Nitrile Rubber (NBR): Highly resistant to oils and fuels, often used in environments where contact with petroleum products occurs.
Silicone Rubber (VMQ): Provides outstanding high and low temperature resistance and flexibility but generally has lower mechanical strength.
EPDM Rubber: Excellent resistance to heat, ozone, and weathering; commonly used in HVAC and outdoor equipment.
2. Metal Components
The metal parts serve as the structural interface for mounting and transferring loads. Materials typically include:
Steel: Most common due to strength and cost-effectiveness; often coated or plated to prevent corrosion.
Stainless Steel: Used in corrosive or marine environments where rust resistance is critical.
Aluminum: Selected for lightweight applications requiring corrosion resistance but less strength compared to steel.
3. Bonding Agents
A critical part of the mount is the adhesive that bonds rubber to metal. High-quality vulcanization and bonding processes ensure long-lasting adhesion and prevent delamination under load or environmental stress.
4. Surface Treatments
Metal surfaces may be treated with phosphate coatings, galvanizing, or powder coatings to enhance corrosion resistance and durability, especially for outdoor or harsh industrial environments.